API ajuda ŠKODA Auto Volkswagen India a instalar linhas de soldagem robótica de nível
MSP segue processo de 4 etapas para garantir a precisão da instalação
A principal fábrica da Volkswagen na Índia produz centenas de milhares de automóveis por ano como parte de sua parceria com a ŠKODA. À medida que a planta se move em direção a processos automatizados de soldagem de corpo inferior, eles precisavam instalar linhas robóticas de soldagem de até 90m de comprimento. Eles recorreram à equipe da API Services para obter apoio. Usando Radian Plus e vProbe, a equipe experiente de Metrólogos da API Services foi capaz de:
- Reduza os erros para um máximo de 0,2mm ao longo dos 90m de comprimento do trilho
- Introduza um processo de instalação rápido e simples de 4 pontos
- Instalação completa de 30 levantadores e 15 luminárias
ŠKODA Auto Volkswagen India Pvt Ltd é a subsidiária indiana integral da fabricante automotiva alemã Volkswagen Group. Foi formada em outubro do ano passado, quando o Volkswagen Group Sales India Pvt Ltd (NSC) e a ŠKODA Auto India Pvt Ltd (SAIPL) foram fundidas em uma única entidade com sede em Pune, Índia.
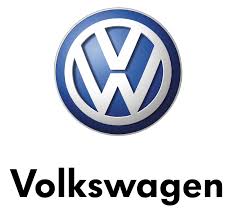
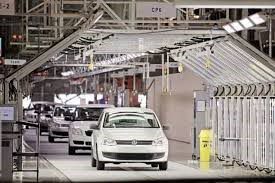
Nesta sede, a Volkswagen India opera uma fábrica em Pune (Chakan) Maharashtra, que é capaz de produzir 200.000 veículos por ano. Junto com a fabricação do Volkswagen Polo e Vento (e o recém-lançado Volkswagen Ameo), a fábrica agora é compartilhada pela ŠKODA para a fabricação do ŠKODA Rapid. A fim de acomodar os veículos adicionais para a ŠKODA, a fábrica passou imediatamente por expansões planejadas para suas operações de soldagem automatizada.
A fábrica começou a instalar linhas robóticas de soldagem com 90m de comprimento. Inicialmente, os layouts das linhas foram marcados por dois engenheiros usando uma fita de medição em cada extremidade da localização da linha. Eles seguravam a fita nas direções X e Y do trilho e combinavam com os locais um do outro. O processo foi demorado e, a uma distância de 90m, os erros eram inevitáveis. Para acelerar o processo e garantir a precisão, a fábrica contratou os Serviços de API para entrar e verificar o layout, instalação e nivelamento dos trilhos de soldagem.
A Equipe de Serviços da API na Índia completou três linhas de soldagem robótica para Underbody 1.1, 2.1 e 2.2, cada uma com 90 metros de comprimento. A equipe da API completou 30 elevadores e 15 jogos. Usando o Radian Plus Laser Tracker com acessório vProbe, a API Services criou o procedimento de 4 etapas seguintes para acelerar o processo, reduzindo os erros máximos de posicionamento para 0,2 mm ao longo da faixa ferroviária de 90m.
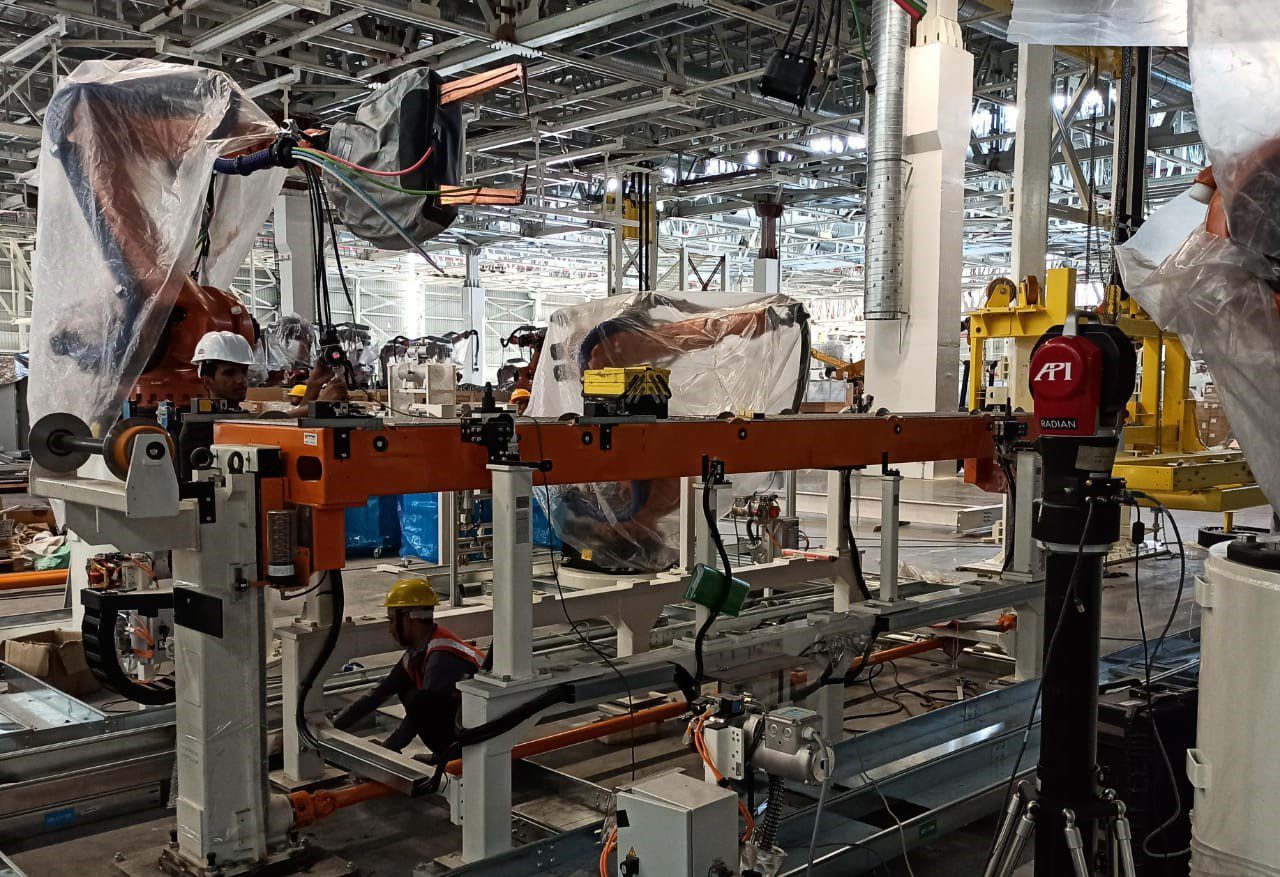
- MARCAÇÃO DE LAYOUT.
Inicialmente, a linha central foi desenhada no chão considerando a distância dada do feixe nos dados de desenho desenhados. Em seguida, um ponto de origem (0,0) foi marcado no chão. Este método foi utilizado para alinhamento plano, linha e pontos. As marcas no chão para a posição das placas base para elevadores, robôs, luminárias, colunas e bandeja de cabos foram todas feitas com a ferramenta de perfuração central (produto API) e as leituras dro do software.
Após a marcação do layout, as placas base foram rejuladas, e os elevadores foram instalados sobre eles. O mesmo alinhamento foi utilizado para configurações de levantador. Aqui a linha central do levantador deve combinar com a linha central para o eixo Y no chão. Como o piso estava irregular, o ponto mais alto do piso foi considerado zero para o levantador. Este valor zero foi usado como um valor de referência para nivelar os outros elevadores usando a opção de plano virtual no software do Tracker para o eixo Z. Finalmente, a distância entre os dois levantadores foi mantida ao longo do eixo X.
- CONFIGURAÇÃO DA INSTALAÇÃO
Aqui o Alinhamento foi feito em relação aos dados do carro zero (método PLP) dado pela equipe de design dos elevadores. Uma vez terminado o alinhamento, o nivelamento das luminárias foi feito pela opção plano virtual/plano de gravidade no software Tracker para as leituras do eixo Z. Em seguida, os Aparelhos foram fisicamente movidos nas direções X e Y para manter sua posição rejulada.
- PINOS E CONFIGURAÇÃO MYLAR
Uma vez que a luminária foi posicionada, mylars e pinos foram medidos com um SMR ou vProbe. Essas leituras foram comparadas com os dados do CAD. Se ocorreram desvios, foram registrados, e correções foram feitas por shimming. Pinos adicionais e mylars no punho robótico foram movidos para suas localizações, com valores medidos pelo SMR ou vProbe, e quaisquer desvios foram corrigidos por shimming. Foram tomadas medidas finais para verificação e relatório.
- TRILHA DA CARROCERIA DO CARRO
Quando as luminárias, mylars e pinos foram alinhados corretamente, o respectivo modelo de carroceria foi mantido na luminária e testado pela equipe da Volkswagen para garantir o devido nivelamento e adesão aos modelos CAD.
A combinação única de metrólogos experientes da API Services com proficiência em todas as indústrias de fabricação e equipamentos de metrologia dimensional de última geração permitiu que eles garantissem a instalação e o nivelamento da Volkswagen com um processo rápido e eficiente. A API lidera o campo de metrologia em todo o mundo há 30 anos. Eles são uma empresa que desenvolve os produtos e tecnologias de metrologia mais avançados e permite que seus usuários obtenham resultados mais precisos e confiáveis. Por mais de 10 anos, a equipe de Serviços Técnicos da API India forneceu laser trackers com mais recursos, bem como serviços de calibração para fabricantes na Índia.
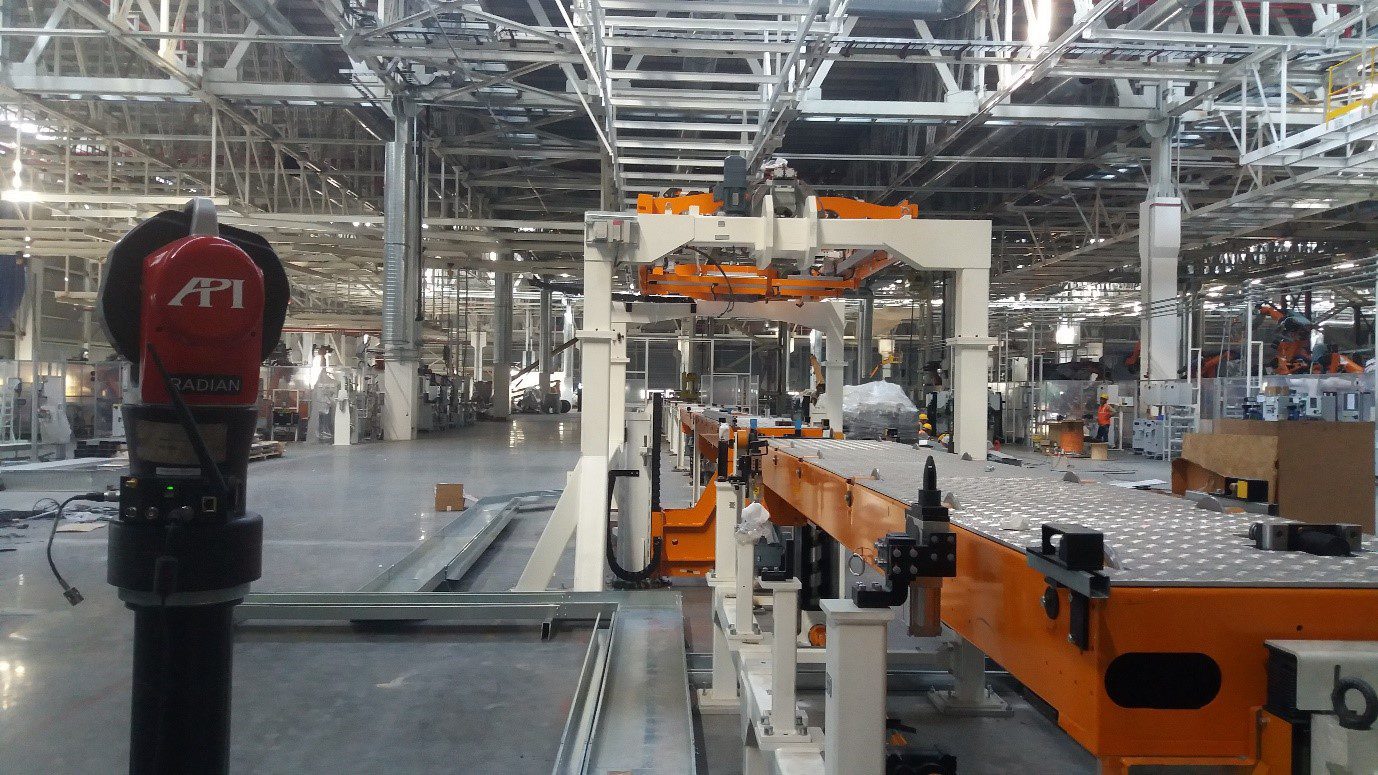
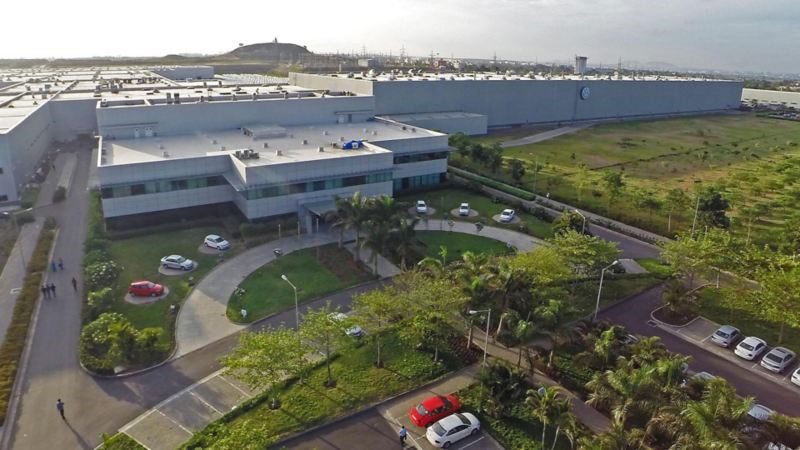
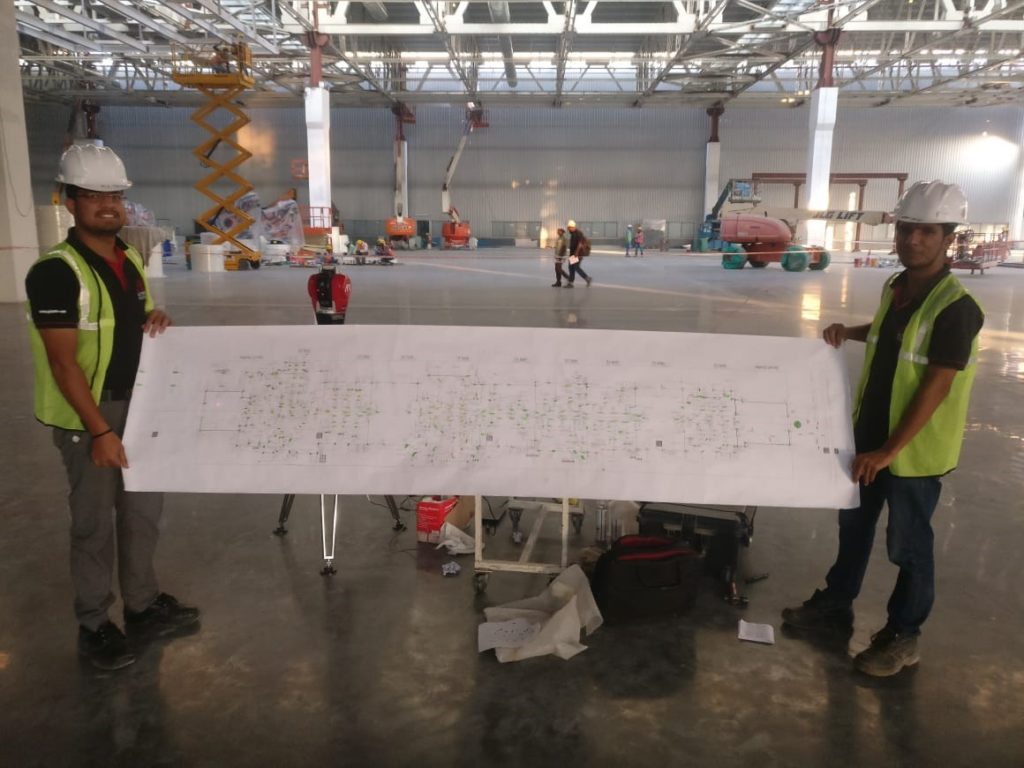
Links deste artigo: