Wenn wir über Industrieroboter sprechen, neigen wir dazu, sie als Werkzeuge zu betrachten, die in den 80er Jahren auf den Plan traten, als voll ausgebildete Vorboten der Industrie 4.0-Bewegung, die im Namen von Geschwindigkeit und Effizienz die Fertigung automatisieren sollte. Aber die Roboter dieser Ära, die anfingen, Automobilfabriken mit immer höheren Stückzahlen zu besetzen, waren bereits ein Produkt jahrzehntelanger Verfeinerung. Der erste Industrieroboter wurde tatsächlich 1938 hergestellt. Er bestand vollständig aus Meccano-Teilen und konnte so programmiert werden, dass er Holzklötze in Mustern stapelte. Und das erste Industrieroboter-Patent wurde 1954 von George Devol für Unimation angemeldet und 1961 erteilt. Es folgten der vollelektrische Stanford-Arm 1969 und die in den 70er Jahren aufkommende Ausbreitung europäischer, japanischer und amerikanischer Robotikunternehmen.
In den fast 60 Jahren der Entwicklung, Produktion und Leistung von Industrierobotern ist jedoch ein wesentliches Problem geblieben: Roboter haben eine ausgezeichnete Wiederholbarkeit, aber ihre Genauigkeit verhindert, dass sie genau sind. Wie wir in diesem Blog erörtert haben, muss man, um wirklich genau zu sein, einem gewünschten Punkt während der gesamten zu erfüllenden Aufgabe durchgehend wiederholbar treu sein. Dieser Mangel an wahrer Genauigkeit hat die Anwendungen, die Industrieroboter ausführen können, eingeschränkt und sie davon abgehalten, ihr volles Potenzial zu erreichen, insbesondere in Branchen, die höchste Toleranzanforderungen stellen.
In den letzten Jahren hat die Kalibrierung von Industrierobotern große Fortschritte gemacht, um das volle Potenzial dieser Maschinen auszuschöpfen. Ein Laser Tracker, der mit einem Smart Track Sensor (STS) oder einer Reihe von kugelförmig montierten Reflektoren (SMR), die am Endeffektor des Roboters montiert sind, arbeitet, kann die absolute Position des Roboters überwachen, während er seine Bahnen durchläuft. Die Kalibriersoftware kann dann diese gesammelten Daten mit dem DH-Kinematikmodell vergleichen und Korrekturen in der Roboterbahn und -position direkt an die Maschinensteuerung übermitteln. Diese Leistungstests und Korrekturen werden in Übereinstimmung mit den ISO 9283-Normen durchgeführt.
Zusätzlich zu den Verbesserungen der Grundgenauigkeit gibt es mehrere Gründe, Ihren Industrieroboter heute zu kalibrieren:
Erweiterte Anwendungsbereiche
Wie oben erwähnt, hat der Mangel an echter Genauigkeit die Implementierung vieler Roboteranwendungen über den Teach-Modus hinaus eingeschränkt. Mit der richtigen Kalibrierung zur Verbesserung der Positionierung und der Pfadpläne öffnen sich Industrieroboter für eine Vielzahl anderer Anwendungen, einschließlich Inspektion, Bearbeitung, Bohren und 3D-Druck. Diese verbesserten Genauigkeiten aus der Kalibrierung können sogar den Einsatz von Robotern in Industrien mit höchsten Toleranzen, wie z.B. im Werkzeugbau der Luft- und Raumfahrt, ermöglichen. Und ihre unübertroffene Wiederholgenauigkeit macht sie schneller und effizienter bei der Durchführung dieser Art von Inspektionsaufgaben.
Individualisierte Leistung
Wie jedes Serienprodukt werden Roboter desselben Modells mit identischen Nennleistungsparametern für jeden Roboter dieses Modells gebaut und geliefert. Im Gegensatz zu anderen Massenprodukten können jedoch die vielen beweglichen Teile und Gelenke für Industrieroboter und andere Einflüsse wie Installationsverfahren und Umgebungsfaktoren zu einer viel größeren Varianz in der individuellen Roboterleistung führen, selbst wenn die Leistung noch genau ist. Die Roboterkalibrierung kann helfen, genaue Parameter für jeden einzelnen Roboter in Ihrer Fabrik zu ermitteln.
Wiederhergestellte Leistung
Selbst bei Robotern, die in der Vergangenheit zuverlässig und wiederholbar waren, muss ihre Leistung routinemäßig gemessen werden, um eine kontinuierliche Qualität zu gewährleisten. Wie alle anderen mechanischen Geräte verlieren auch Roboter im Laufe der Zeit natürlich an Leistung und damit an Genauigkeit, sei es durch natürlichen Verschleiß oder durch eine Kollision oder ein unerwartetes Abschalten. Bei ereignisbasierten Leistungseinbußen wie einer Kollision oder natürlichen Erosion im Laufe der Zeit kann eine regelmäßige planmäßige Kalibrierung dazu beitragen, die Genauigkeit und Leistung des Roboters wiederherzustellen. Diese Überprüfungen können kleine Fehler erkennen und korrigieren, bevor sie groß genug werden, um die Leistung zu beeinträchtigen, Ausfallzeiten und kostspielige Nacharbeiten reduzieren und die Lebensdauer Ihres Roboters verlängern.
Industrieroboter sind traditionell in ihren Einsatzmöglichkeiten für Produktionen mit strengen Toleranzen begrenzt, da sie zwar wiederholbare Leistungen erbringen, aber nicht die für eine echte Genauigkeit erforderliche Positionsgenauigkeit aufweisen. Laser Tracker können jedoch in Verbindung mit STS oder SMR und spezieller Software eingesetzt werden, um die Roboterleistung zu verfolgen, die Genauigkeit zu verbessern oder wiederherzustellen, ihre Anwendungen zu erweitern und individuelle Nennparameter für jeden einzelnen Roboter zu erstellen.
API’s Robot Metrology Solution (RMS) bietet eine komplette Lösung zur Verbesserung von Robotern, die den 6DoF Radian Laser Tracker mit dem Smart Track Sensor (STS) und proprietärer Software zur Bewertung der Roboterleistung kombiniert. RMS verwendet 14 statische und dynamische Tests zur Bewertung von Robotern gemäß ISO 9283-Standard, aktualisiert das kinematische DH-Modell und führt eine volumetrische Fehlerkompensation durch, um die Genauigkeit und Bahnplanung zu verbessern. Und für all Ihre Kalibrieranforderungen (einschließlich Laser Tracker, Werkzeugmaschinen und KMGs) steht das Team erfahrener Messingenieure von API Services an jedem unserer global-lokalen Standorte zur Verfügung.
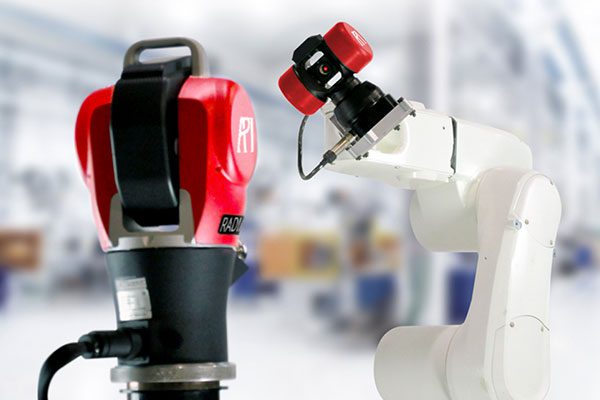
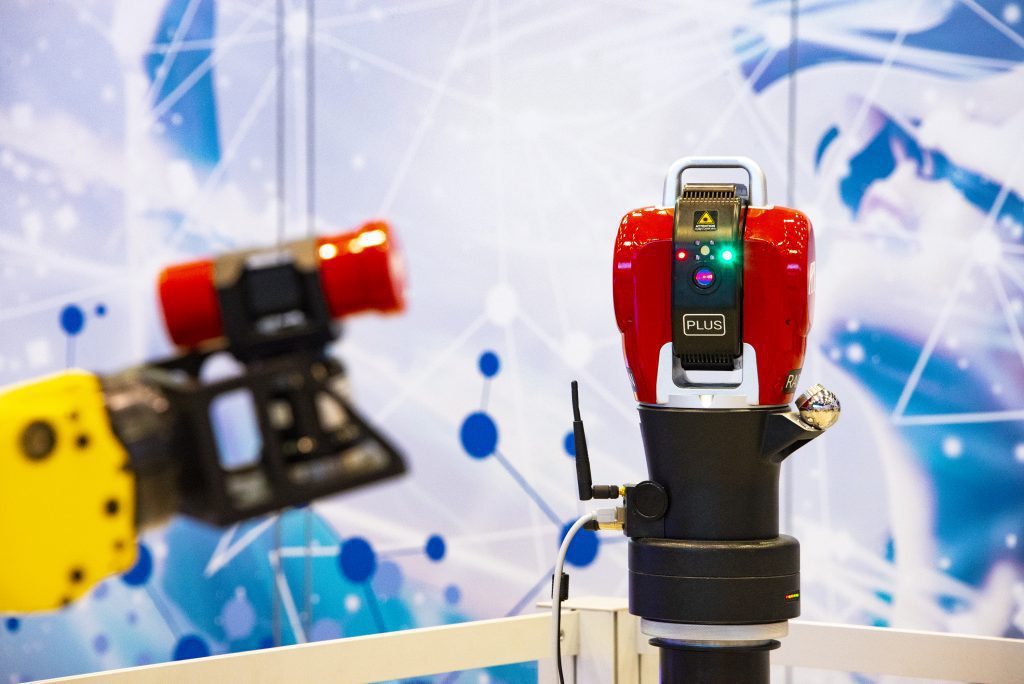
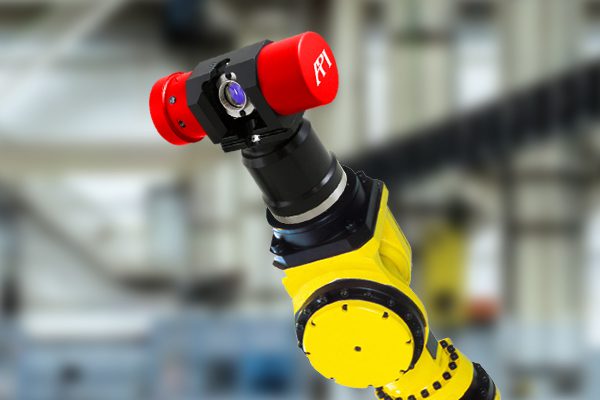