API hilft ŠKODA AUTO Volkswagen India bei der Installation und Ausrichtung von Roboterschweißlinien
MSP folgt einem 4-Schritte-Prozess, um die Genauigkeit ab der Installation zu sicherzustellen
Das Hauptfertigungswerk von Volkswagen in Indien produziert im Rahmen der Partnerschaft mit ŠKODA jährlich Hunderttausende von Automobilen. Da sich das Werk auf automatisierte Unterbodenschweißverfahren umstellt, mussten Roboterschweißlinien mit einer Länge von bis zu 90 m installiert werden. Sie wandten sich zur Unterstützung an das Team von API Services. Mit Hilfe vom Radian Plus und der vProbe konnte das erfahrene Team von Metrologen bei API Services diese Aufgabe bewältigen:
- Reduzierung der Fehler auf ein Maximum von 0,2 mm über die 90 m Länge der Linie
- Einführung eines schnellen und einfachen 4-Punkt-Installationsprozesses
- Vollständige Einrichtung von 30 Hebern und 15 Vorrichtungen
ŠKODA AUTO Volkswagen India Pvt Ltd ist die hundertprozentige indische Tochtergesellschaft des deutschen Automobilherstellers Volkswagen Group. Sie wurde im Oktober letzten Jahres gegründet, als Volkswagen Group Sales India Pvt Ltd (NSC) und ŠKODA AUTO India Pvt Ltd (SAIPL) zu einer Einheit mit Sitz in Pune, Indien, fusionierten.
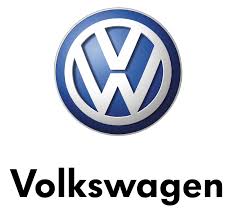
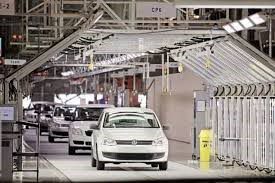
An diesem Hauptsitz betreibt Volkswagen Indien eine Produktionsstätte in Pune (Chakan) Maharashtra, die in der Lage ist, 200.000 Fahrzeuge pro Jahr zu produzieren. Zusammen mit der Fertigung von Volkswagen Polo und Vento (und dem neu eingeführten Volkswagen Ameo) wird das Werk nun von ŠKODA zur Herstellung des ŠKODA Rapid gemeinsam genutzt. Um die zusätzlichen Fahrzeuge für ŠKODA unterbringen zu können, wurde das Werk sofort einer geplanten Erweiterung der automatisierten Schweißarbeiten unterzogen.
Das Werk begann mit der Installation von Roboterschweißlinien, die 90 m lang waren. Zu Beginn wurden die Layouts für die Linien von zwei Ingenieuren mit einem Maßband an beiden Enden der Linie markiert. Sie hielten das Maßband in X- und Y-Richtung der Linie und passten die Positionen zueinander an. Das Verfahren war zeitaufwändig, und bei einer Reichweite von 90 m waren Fehler unvermeidlich. Um den Prozess zu beschleunigen und die Genauigkeit zu gewährleisten, beauftragte das Werk API Services mit der Aufgabe, das Layout auf den Boden zu markieren, die Installation und die Ausrichtung der Schweißschienen.
Das India Services Team von API stellte drei Roboterschweißlinien für Unterboden 1.1, 2.1 und 2.2 fertig, die jeweils 90 Meter lang sind. Das Team hat 30 Heber und 15 Vorrichtungen fertiggestellt. Unter Verwendung des Radian Plus Laser Tracker mit vProbe-Zubehör schuf API Services das folgende 4-Schritt-Verfahren, um den Prozess zu beschleunigen und gleichzeitig die maximalen Fehler bei der Positionierung auf 0,2 mm über den 90 m langen Schienenbereich zu reduzieren.
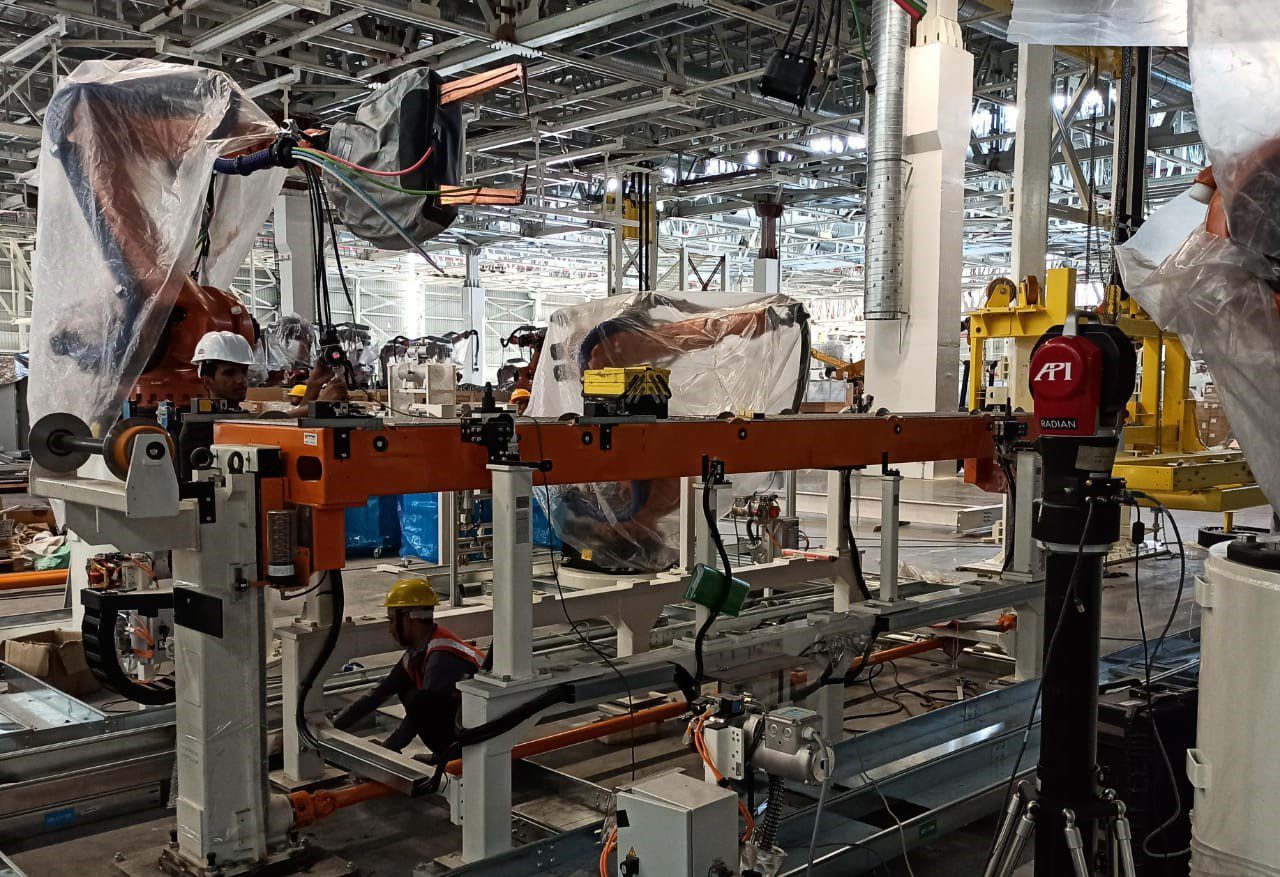
LAYOUTMARKIERUNG
Zunächst wurde die Mittellinie auf dem Boden unter Berücksichtigung des gegebenen Abstandes der Träger in den gezeichneten Konstruktionsdaten erstellt. Dann wurde ein Ursprungspunkt (0,0) auf dem Boden markiert. Diese Methode wurde für die Ausrichtung von Ebene, Linie und Punkte verwendet. Die Markierungen auf dem Boden für die Position der Grundplatten für Heber, Roboter, Vorrichtungen, Aufständerungen und Kabelkanal wurden alle mit einem Körnerwerkzeug (API-Produkt) und den DRO-Messwerten aus der Software vorgenommen.
Nachdem die Grundrissmarkierungen angebracht waren, wurden die Bodenplatten verfugt und die Heber darauf installiert. Die gleiche Ausrichtung wurde für die Heber-Einstellungen verwendet. Hier sollte die Mittellinie der Heber mit der Mittellinie für die Y-Achse auf dem Boden übereinstimmen. Da der Boden uneben war, wurde der höchste Punkt auf dem Boden für den Heber als Nullpunkt betrachtet. Dieser Nullwert wurde als Referenzwert verwendet, um die anderen Heber mit Hilfe der Option “Gravitationsebene” in der Tracker-Software für die Z-Achse zu nivellieren. Schließlich wurde der Abstand zwischen den beiden Hebern entlang der X-Achse beibehalten.
POSITIONIERUNG DER VORRICHTUNG
Hier wurde die Ausrichtung in Bezug auf den Fahrzeugnullpunkt (PLP-Methode) vorgenommen, die vom Konstruktionsteam angegeben wurden. Nach Abschluss der Ausrichtung erfolgte die Nivellierung der Vorrichtungen durch die Option “Gravitationsebene” in der Tracker-Software für die Messungen der Z-Achse. Dann wurden die Spannvorrichtungen physisch in X- und Y-Richtung bewegt, um sie auf ihre vorgesehene Lage zu positionen und befestigen.
- VERIFIZIERUNG DER VORRICHTUNG – MESSUNG DER ZENTRIERUNGEN UND KONTURE
Nachdem die Vorrichtung positioniert war, wurden Zentrierungen und Konturen mit einer SMR oder vProbe gemessen. Diese Messwerte wurden mit CAD-Daten verglichen. Falls Abweichungen auftraten, wurden diese aufgezeichnet und Korrekturen wurden durch shimsen vorgenommen. Zusätzliche Stifte und Konturen auf dem Roboterarmgreifer wurden mit den von der SMR oder vProbe gemessenen Werten an ihre Positionen bewegt und alle Abweichungen wurden ebenso durch shimsen korrigiert. Es wurden abschließende Messungen für die Verifizierung und den Bericht vorgenommen.
KAROSSERIESPUR
Wenn die Halterungen, Mylars und Stifte richtig ausgerichtet wurden, wurde das jeweilige Karosseriemodell auf der Halterung gehalten und vom Volkswagen Team getestet, um eine ordnungsgemäße Nivellierung und Einhaltung von CAD-Modellen zu gewährleisten.
Die einzigartige Kombination von erfahrenen Metrologen mit Kenntnissen in allen Fertigungsindustrien und modernster Maßmesstechnik-Ausrüstung von API Services ermöglichte es ihnen, die Installation und Nivellierung von Volkswagen mit einem schnellen und effizienten Prozess zu gewährleisten. API ist seit 30 Jahren weltweit führend im Bereich der Messtechnik. Sie sind ein Unternehmen, das die fortschrittlichsten Messtechnikprodukte und -technologien entwickelt und es ihren Benutzern ermöglicht, präzisere und zuverlässigere Ergebnisse zu erzielen. Seit über 10 Jahren liefert das Technische Service-Team von API India Laser Tracker mit den meisten Funktionen sowie Kalibrierservices für Hersteller in Indien.
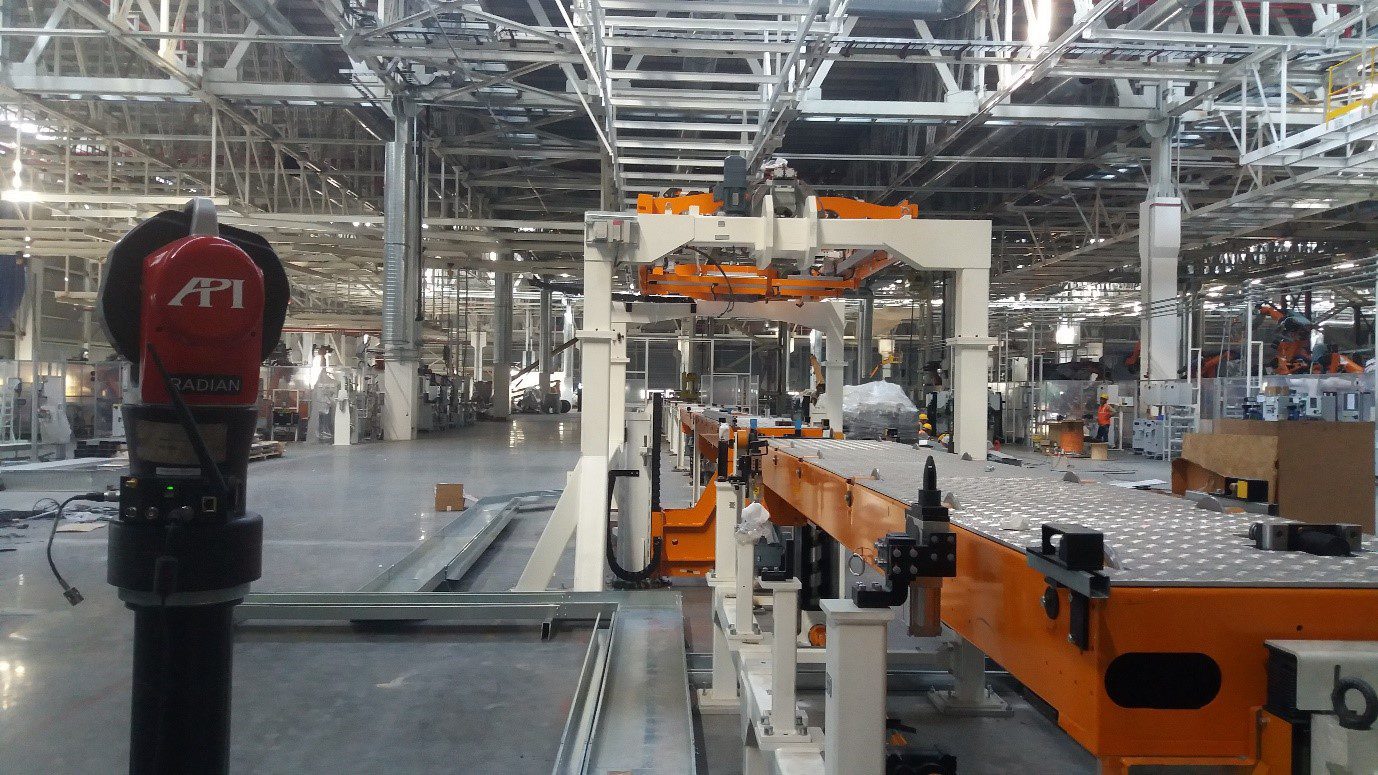
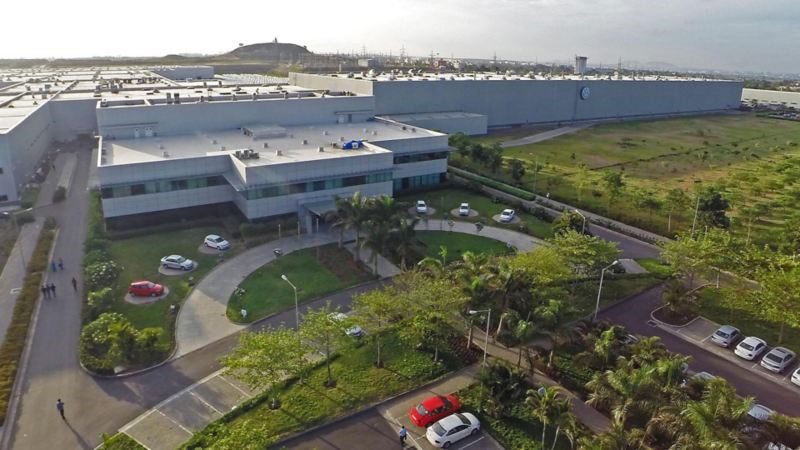
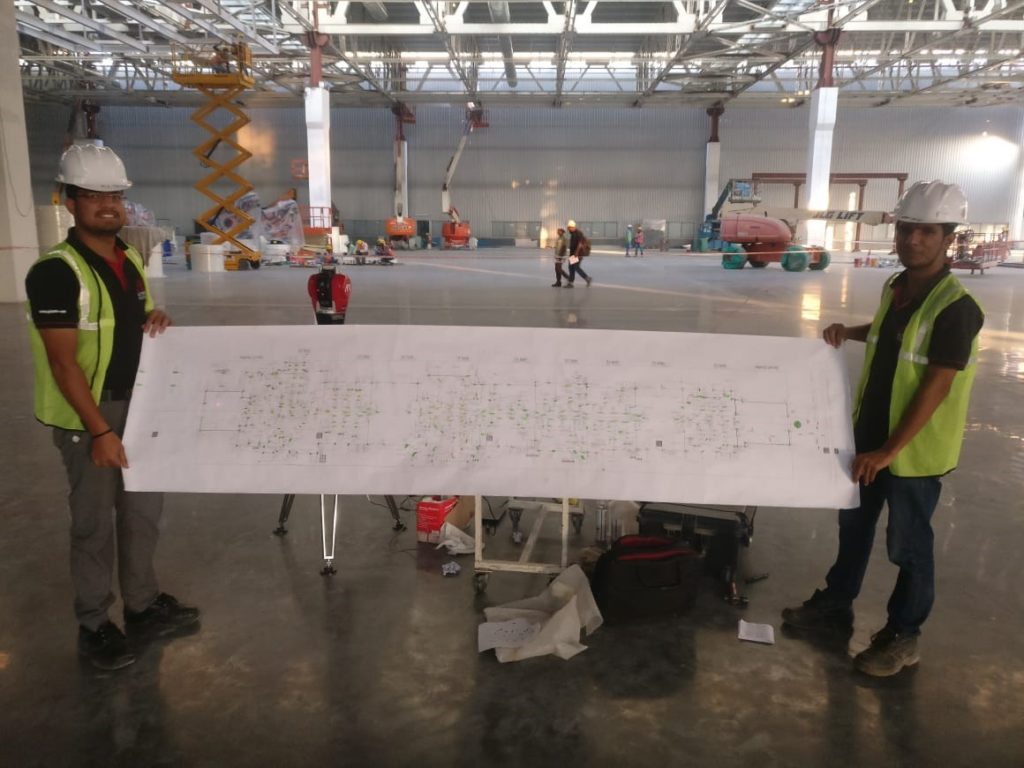
Links aus diesem Artikel: