7 Gründe, Ihre Werkzeugmaschine heute zu kalibrieren
Jede Branche, unabhängig vom Umfang ihrer Arbeit, hat Projekte im Bereich des industriellen Ingenieurwesens, die ihre Wurzeln in der Werkzeugmaschinenproduktion haben. CNCs, Drehmaschinen, Mehr-Achs-Systeme und vieles mehr werden überall eingesetzt, von der Luft- und Raumfahrt über die Automobilindustrie und Schwerindustrie bis hin zum Verteidigungs- und Schiffsbau. Die Projekte in diesen Bereichen erfordern sehr genaue Toleranzen, oft bis auf wenige Mikrometer genau. Die Werkzeugmaschinen, die in diesen Produktionen eingesetzt werden, müssen also nach denselben Standards genau sein.
Zusätzlich zu den Umgebungseinflüssen, wie Fundament, Montage, Ausrichtung und Temperatur, gibt es bis zu 21 Fehlerparameter für eine einfache dreiachsige Werkzeugmaschine. Die lineare Positionierung, die vertikale und seitliche Geradheit sowie die Neigung, das Rollen und das Drehen haben alle Fehlermöglichkeiten in ihren X-, Y- und Z-Koordinaten. Außerdem können Werkzeugmaschinen Fehler erzeugen, wenn sie an den XY-, YZ- und XZ-Koordinatenübergängen nicht perfekt rechtwinklig sind.
Wenn sie nicht erkannt und verhindert werden, können diese Fehler die Qualität von Gussteilen, Werkzeugen, Baugruppen und Verbundwerkstoffen für ein bestimmtes Projekt beeinträchtigen und zu kostspieligen Nacharbeiten oder zur Verschrottung von Teilen führen. Glücklicherweise können diese Fehler gefunden und kompensiert werden, bevor sie zu Projektverzögerungen oder zur Verschrottung von Teilen führen. Die gebräuchlichste Form der Werkzeugmaschinenkalibrierung (MTC) ist die Verwendung eines Laserinterferometers, aber es gibt auch andere Methoden, darunter Ballbars und Swivel Checks oder die Verwendung eines Laser Tracker für die vollständige volumetrische Fehlerkompensation (VEC). Jede dieser Methoden hat ihre eigenen Vorteile für verschiedene Maschinentypen und -aufstellungen, aber alle sind nützlich für die notwendige Arbeit zur Verhinderung oder Beseitigung von Werkzeugmaschinenfehlern.
Im Folgenden finden Sie die 7 wichtigsten Gründe, um Ihre Werkzeugmaschine noch heute kalibrieren zu lassen:
1) Abnahmeprüfung
Die Abnahmeprüfung ähnelt der Laser Tracker-Zertifizierung. Dabei wird die Leistung einer Werkzeugmaschine anhand der vom OEM angegebenen Spezifikationen gemessen, um die Leistung des Werkzeugs zu validieren. Diese eignen sich ideal für Maschinen, die gerade erst installiert wurden (selbst neue Maschinen sind in bis zu 88% der Fälle nicht ausgerichtet) oder die bei kürzlich durchgeführten Projekten noch nicht in Betrieb waren. Das Ziel ist es, Fehler (oder das Potenzial dafür) zu finden, bevor eine wertvolle Bearbeitung stattfindet.
2) Vorbeugende Wartung
Ähnlich wie beim Abnahmetest geht es bei der vorbeugenden Wartung darum, Fehlerquellen zu identifizieren und zu beseitigen, bevor sie sich auf die Produktionsergebnisse auswirken. Ähnlich wie beim Ölwechsel bei einem Auto geht es bei der vorbeugenden Wartung von Werkzeugmaschinen darum, routinemäßige und planmäßige Überprüfungen der Maschinen durchzuführen, auch wenn diese keine erkennbaren Fehler aufweisen. Fehler bereits in diesem Stadium zu erkennen, erspart kostspielige Ausfallzeiten und Nacharbeiten zu einem späteren Zeitpunkt im Prozess.
3) Zertifizieren Sie eine Maschine, die über Antastfunktion verfügt
Werkzeugmaschinen, die über Antastfunktionen verfügen, stellen eine zusätzliche Quelle für mögliche Winkelablenkungsfehler dar. Wenn die Bewegung des Messtasters fehlerhaft ist, zeigen die Ergebnisse des Messtasters einen Fehler an, der häufig in lineare Fehlerdaten verschmilzt. Diese Fehler können schwer zu diagnostizieren und von Problemen in der Bahn des Werkzeugs zu unterscheiden sein, aber sie können durch eine ordnungsgemäße Kalibrierung sowohl linear als auch winklig kompensiert werden.
4) Kennen Sie die Genauigkeitsgrenzen Ihrer Maschine
Regelmäßige Maschinenkalibrierung ist auch eine Möglichkeit, die Grenzen Ihrer Werkzeugmaschine in einer Situation mit geringerem Einsatz zu testen. Indem Sie Ihr Werkzeug in einer Kalibrierungseinstellung auf die Einhaltung seiner engsten Toleranzen oder seines maximalen Fertigungsumfangs einstellen, können Sie die äußeren Grenzen seiner Kapazität ermitteln (selbst bei Anwendung von Kalibrierung und Kompensation), ohne ein Teil zu erzeugen, das möglicherweise nachbearbeitet oder verschrottet werden muss.
5) Verbessern Sie die Genauigkeiten auf älteren Maschinen
Wie bei allen mechanischen Komponenten verschlechtert sich die Leistung von Werkzeugmaschinen oft mit der Zeit. Eine regelmäßige Kalibrierung kann jedoch oft viele dieser Fehler korrigieren und die Lebensdauer Ihrer Werkzeugmaschine verlängern. Bevor Sie in den kostspieligen und zeitraubenden Prozess des Austauschs eines alten Werkzeugs einsteigen, kann eine ein- oder zweitägige Kalibrierung durch einen Messtechnik-Dienstleister (MSP) den reibungslosen Betrieb des Werkzeugs sicherstellen.
6) Reduzieren Sie Maschinenausschuss
In Situationen, in denen die aufgetretenen Fehler überschaubar sind, können Teile nachbearbeitet statt verschrottet werden, und das Projekt kann nach einer kurzen Pause fortgesetzt werden. Aber dies ist bestenfalls eine Notlösung. Nacharbeit ist immer noch kostspielig aufgrund der zusätzlichen Zeit, die für die Reparatur der schadhaften Teile und der verschwendeten Materialien aufgewendet wird. Die Maschinenkalibrierung kann die Menge an Nacharbeit und Ausschuss während des gesamten Herstellungsprozesses merklich reduzieren.
7) Präzisere Teile
Schließlich und ganz offensichtlich produzieren Werkzeugmaschinen, die regelmäßig kalibriert und gewartet werden, die präzisesten Teile. Die Genauigkeit in den Anfangsphasen der Produktion (von der Modellierung bis zur ersten Bearbeitung) wirkt sich stufenweise auf den gesamten Prozess aus und beschleunigt die Verifikations-, Änderungs- und Montagephasen. Effiziente Werkzeugmaschinen ermöglichen es, Projekte genau, pünktlich und im Rahmen des Budgets abzuschließen.
Eine regelmäßige und planmäßige Werkzeugmaschinenkalibrierung ist unerlässlich, um die Genauigkeit des Werkzeugs, des Teils und des Projekts als Ganzes zu gewährleisten. Viele Maschinenwerkstätten entscheiden sich für den Kauf von MTC-Ausrüstung (wie XD-Laser und Wireless Ballbar von API) und Schulungen, damit ihre Teams die Arbeiten im eigenen Haus durchführen können, aber für viele ist das nicht die kostengünstigste Lösung. Für die Schulung oder Vertragskalibrierung verfügt API Services über jahrzehntelange Erfahrung mit unserer hochmodernen MTC-Ausrüstung und mit mehr als 20 Arten von Werkzeugmaschinensteuerungen. Klicken Sie hier, um mehr über MTC zu erfahren und Ihren Termin noch heute zu vereinbaren.
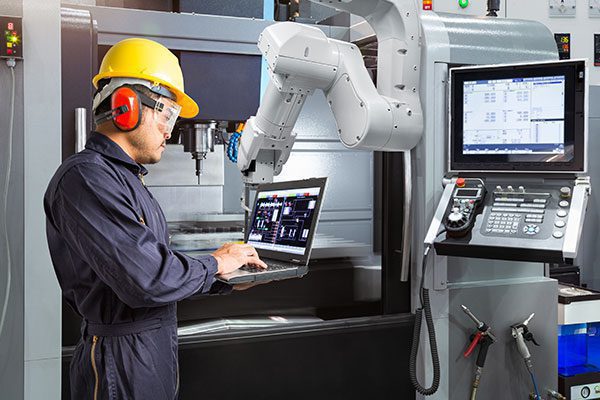


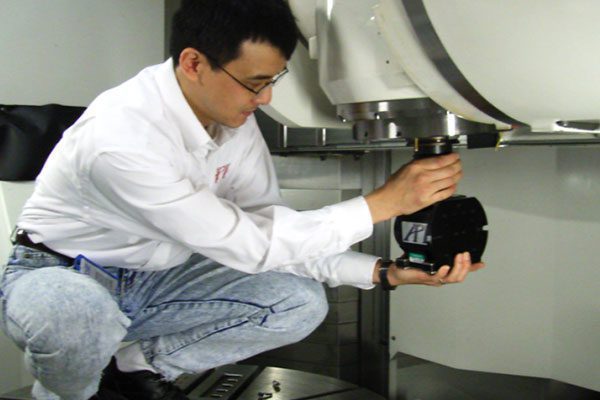
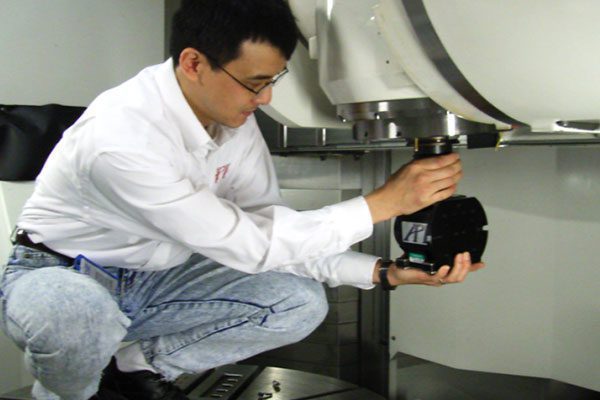
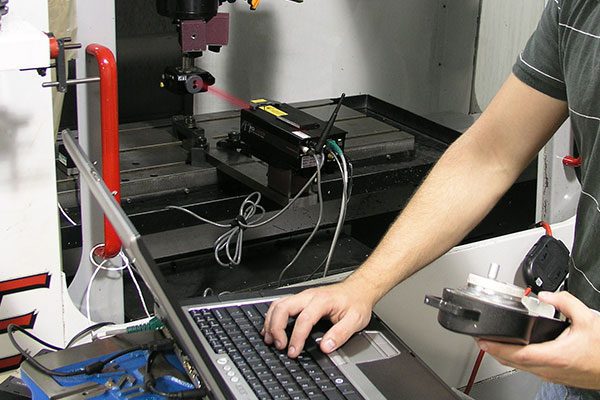
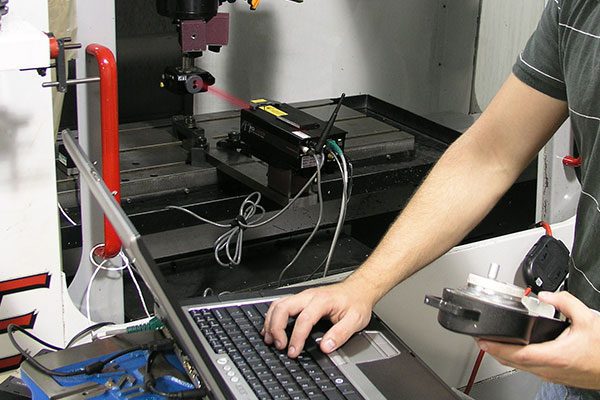
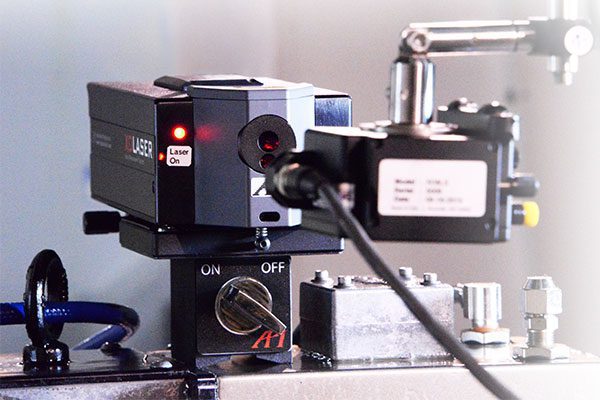
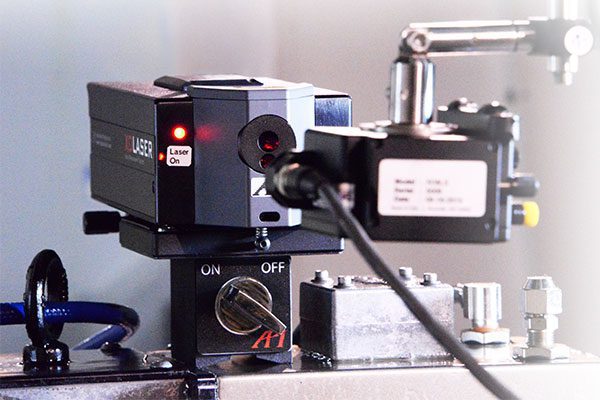