ÉTUDE DE CAS | LASER TRACKER ET VPROBE | VÉHICULES FERROVIAIRES
API and Siemens
La Bogie Lead-Factory de Siemens-Mobility à Graz, centre de développement et usine de fabrication de bogies de haute technologie, est un partenaire important de l’industrie mondiale des véhicules ferroviaires. Qu’il s’agisse de bogies pour tramways, locomotives, voitures de voyageurs ou automotrices à grande vitesse, le Siemens Mobility World Center of Excellence for Bogie Technology couvre toute la gamme de produits pour le trafic au sol. La productivité élevée représente un degré d’automatisation unique au monde. L’utilisation de la technologie dans la production mécanique en particulier établit de nouvelles normes – pour la configuration et le serrage, les cadres de châssis sont déjà mesurés avec succès depuis de nombreuses années à l’aide de solutions de mesure API. Depuis 2022, ils sont mesurés à l’aide de la dernière génération du Radian Laser Tracker et du capteur 3D sans fil vProbe, offrant :
- • Mesure d’encastrement jusqu’à 30 mm avec stylet étendu
- • Mesures de suivi montées pour la stabilité et la disponibilité
- • Flux de travail automatisé pour prendre en charge les opérations de quart.
Au début se trouve la configuration
L’une des compétences clés de l’usine de Graz est le traitement mécanique des cadres et des composants du châssis, en commençant par l’alignement des composants sur des montages modulaires. Afin d’atteindre un débit de production plus élevé, la technologie de mesure devait également suivre le rythme de la capacité de production, ce qui nécessitait finalement de nouveaux systèmes de mesure. L’exigence de base est le fonctionnement de deux postes de serrage sur lesquels les châssis sont alignés en fonctionnement posté, mesurés et serrés sur leurs fixations avec une faible contrainte et sans distorsion pour le traitement mécanique ultérieur.
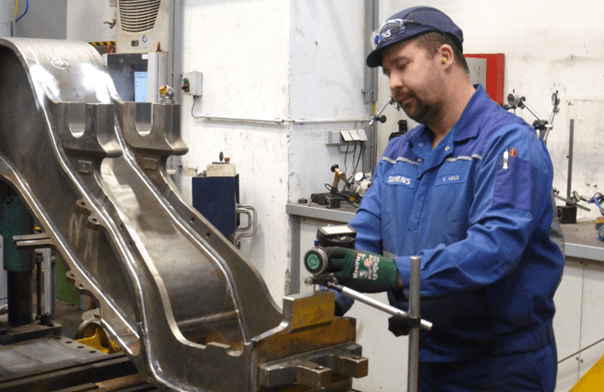
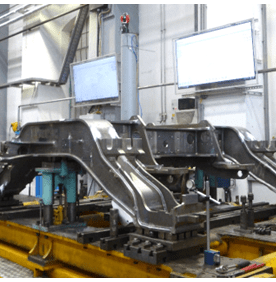
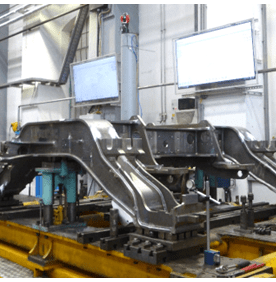
Les lectures du capteur sans fil portable et du laser tracker sont affichées sur de grands écrans LCD
Dans le passé, Siemens-Mobility travaillait avec des jauges à cadran fixées aux fixations de serrage avec des aimants. Dès le début, il était nécessaire de mesurer des points souvent difficiles d’accès – selon le type, jusqu’à 30 points de mesure par chariot, ce qui signifiait beaucoup de temps nécessaire pour la configuration et le serrage. Pour les mesures, jusqu’à 20 cadrans ont été utilisés simultanément par chariot. Au fil du temps, il est devenu évident que cette stratégie de mesure ne serait pas en mesure de suivre le rythme de l’augmentation requise de la production.
Systèmes de mesure modernes – et inconvénients décisifs
Mesurer les points difficiles à atteindre est toujours un défi particulier. Ainsi, les nouveaux systèmes de mesure portables tels que les bras de mesure, qui ne pouvaient pas faire face aux points de mesure définis par la conception, souvent situés à une profondeur de composant de 200 à 300 mm, ont également été exclus ici.
Parallèlement, l’utilisation de laser trackers a été étudiée à Graz, ce qui promettait des précisions encore plus élevées grâce à leurs principes de mesure basés sur le laser. Comme les bras de mesure, les trackers remplacent de plus en plus les systèmes de mesure conventionnels tels que les machines à mesurer tridimensionnelles (MMT).
Mais ici aussi, il s’est avéré que le principe de mesure sans contact des Laser Trackers, qui est avantageux dans de nombreux cas et qui, contrairement aux bras de mesure mécaniques, peut encore être utilisé pour mesurer de très grandes pièces (les cadres de châssis à 3 essieux peuvent mesurer jusqu’à 7 mètres de long), a apporté un inconvénient décisif: Mesure avec le réflecteur monté en surface (SMR), typique des Laser Trackers, ne fonctionnait pas plus dans le contexte des mesures de test chez Siemens-Mobility que de mesurer avec des bras de mesure – dans les renfoncements des cadres de châssis qui devaient être mesurés, la sphère de mesure ne pouvait pas être atteinte par le faisceau laser du tracker et ne pouvait donc pas être mesurée.
Mieux vaut l’ennemi du bien
En principe, la supériorité des systèmes laser a été reconnue, mais aucun des fournisseurs n’a réussi à convaincre la direction de l’usine: les inconvénients des systèmes techniquement similaires, qui différaient toutefois considérablement en taille et en portabilité, étaient trop importants. Les recherches des spécialistes des techniques de mesure à Graz ont pris un tournant décisif avec l’arrivée sur le marché d’une nouvelle génération de capteurs portatifs présentant un avantage significatif par rapport aux PRM standard :
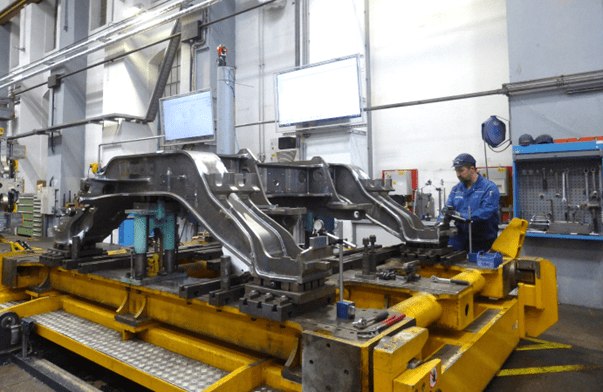
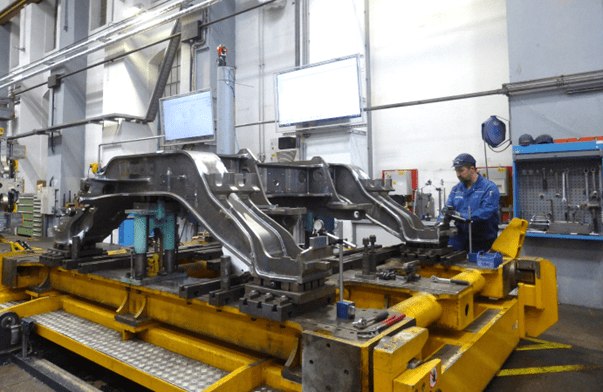
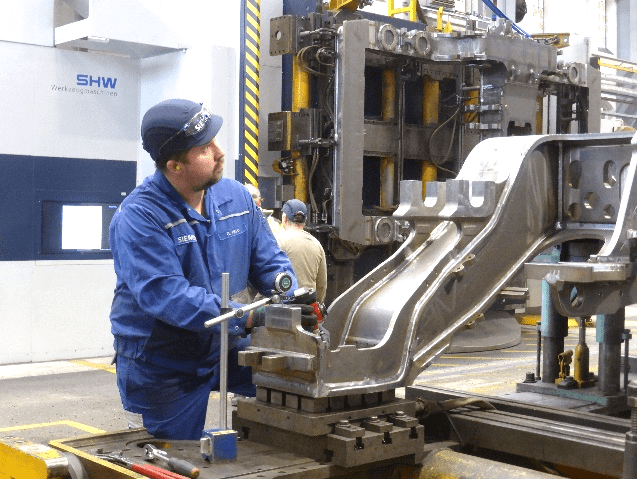
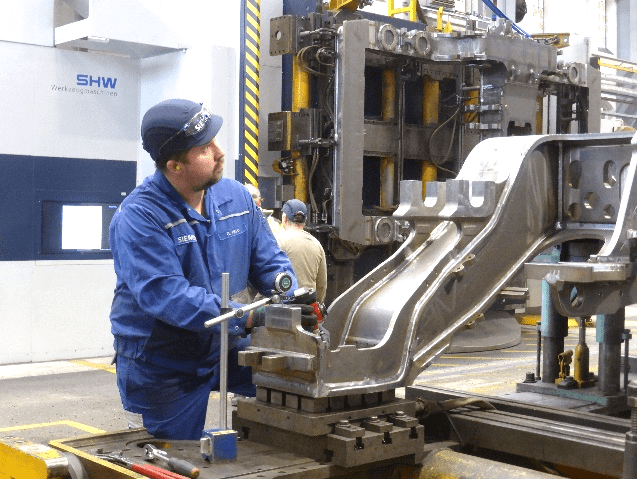
Monté sur une colonne : L’API Laser TrackerÀ droite : Le vProb sans fil
Le vProbe d’API est un capteur sans fil portable et léger avec une sonde qui permet d’inspecter des caractéristiques complexes ou des points cachés pour les pièces volumineuses et complexes. Les capteurs sans fil remplacent les SMR existants dans l’espace de travail du tracker.
En fonction de la longueur de la pointe (avec extension jusqu’à 30mm), il était désormais possible d’atteindre et de mesurer les points des cadres du train d’atterrissage situés dans les renfoncements. Cela a finalement résolu le problème de sondage. Toutefois, afin de suivre le rythme de l’augmentation des capacités de production, des mesures supplémentaires étaient nécessaires de la part de la stratégie de mesure.
La nouvelle stratégie de mesure
Après des tests approfondis, la décision a été prise en faveur du Laser Tracker le plus petit et donc le plus portable, le Radian Laser Tracker d’API. En raison des deux luminaires voisins sur lesquels mesurer et des points de mesure difficiles d’accès, une installation au niveau du sol du système de mesure sur un trépied était hors de question.
Au lieu de cela, le tracker a été monté sur une colonne spécialement érigée à cet effet au milieu entre les positions de serrage à une hauteur d’environ 4 mètres. Il a été décidé de ne pas monter le Laser Tracker sur le mur extérieur du hall après avoir déterminé que les mouvements de la grue causaient des vibrations qui affectaient les mesures.
Le logiciel Polyworks® d’Innovmetric est utilisé pour afficher et contrôler les valeurs mesurées. Ainsi, une solution innovante et en même temps pratique a été trouvée: deux grands écrans LCD montés haut sur le mur du hall permettent de vérifier les valeurs mesurées depuis les deux postes de travail. Le tracker lui-même n’a pas besoin d’être utilisé et reste allumé en permanence.
Processus de mesure automatisés
Mais ce n’était pas la fin de l’histoire. Le degré élevé d’automatisation de l’usine principale de Graz, dont la capacité annuelle maximale est d’environ 4 000 chariots, a nécessité des mesures supplémentaires dans la mise en œuvre métrologique de la configuration et du serrage, qui ont dû suivre le traitement dans différents modèles de postes.
« Ce dont nous avions besoin, c’était de la fiabilité des processus en fonctionnement posté », explique Martin Gruber, responsable de la production mécanique chez Siemens-Mobility à Graz. « Le système de mesure devait guider les employés. Nous avions besoin d’une documentation significative des mesures et de la visualisation des processus. »
Mesure sur de longues distances:
Avec le vProbe, même les points de mesure cachés sont atteints
En raison de l’usinage en équipe, un travailleur qualifié qualifié doit être capable d’effectuer lui-même toutes les mesures – sans le soutien d’un technicien de mesure.
La tâche nécessite un degré élevé d’automatisation des processus de mesure, au sein desquels les spécialistes de Siemens-Mobility, en collaboration avec API, ont non seulement défini tous les types de châssis à produire, mais ont également stocké les étapes de traitement dans l’ordre respectif dans lequel elles devaient être traitées. Cela a également simplifié les mesures.
Selon Martin Gruber, cependant, ce n’était pas seulement le temps de mesure qui pouvait être économisé. La flexibilité et la fiabilité des processus jusqu’à la mesure finale des châssis étaient également importantes. Étant donné qu’un Laser Tracker peut mesurer dynamiquement, il est également possible, entre autres, de vérifier la torsion lorsque le cadre est serré.
Dans l’ensemble, la stratégie de mesure suit donc l’assemblage du cycle chez Siemens-Mobility, qui est basé sur des principes lean et garantit un châssis de haute qualité « juste-à-temps ».
RADIAN Laser Tracker Pro et Plus
Avec leur plage de mesure allant jusqu’à 80 mètres en combinaison avec le vProbe, ils constituent le système le plus compact pour le balayage et le sondage.
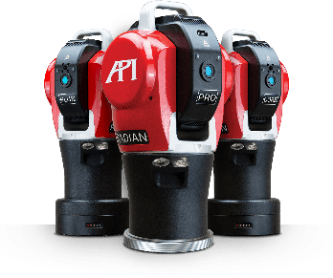
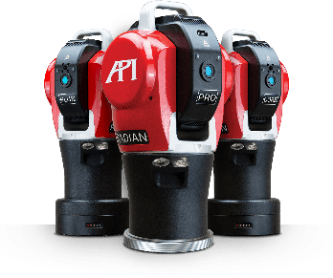
vProbe
Capteur portatif, léger et sans fil, avantageux pour la mesure tactile de points difficiles d’accès et de structures cachées.
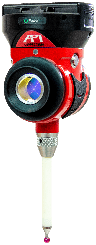
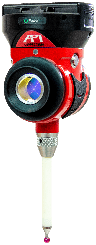
Impatient:
API et Siemens-Mobility se réjouissent de poursuivre leur partenariat à l’avenir afin de maintenir l’usine de Graz à la pointe de la technologie et des processus de mesure laser afin de fournir les résultats de mesure et la productivité les plus rapides et les plus précis possibles. Radian Plus et vProbe d’API fournissent des mesures portables et sans fil dans l’atelier avec une précision CMM depuis plus d’une décennie. Pour en savoir plus sur la façon dont ils peuvent vous aider à prendre en charge vos applications d’inspection, ou pour en savoir plus sur Siemens-Mobility à Graz, visitez les liens ci-dessous.
https://new.siemens.com/at/de/unternehmen/ueber-uns/standorte/standort-steiermark.html
Plus d’informations sur le Radian Laser Tracker :
https://apimetrology.com/radian/
Informations sur le palpage portable avec le vProbe :