API’s 9D LADAR for Automotive In-line Inspection
Executive Summary
API’s recently introduced Dynamic 9D LADAR System with an API 6DoF Radian Laser Tracker can directly support the Automotive Body-in-white (BIW) market and other large dimensional non-contact inspection projects. This solution improves on current Laser Radar offerings in speed, accuracy, flexibility, portability, and repeatability.
Problem Statement
Demand on automotive assembly plants around the world continues to rise for more cars to be made at increasingly tight tolerances, and with the push to build more electric vehicles, these demands will surely continue. According to the Frost & Sullivan 2019 white paper, “A Paradigm Shift of In-line Inspection in Body-in-White,” 97% of sampled industry respondents maintain the “key factor” for Industry 4.0 adoption is to improve internal efficiency.
One such area of focus is the dimensional inspection process, or specifically the “in-line” Body-In-White (BIW) process. BIW is simply the vehicle’s body attached to the frame minus the hinged closures. The industry has pushed to measure BIW while traveling down the assembly line. This concept presents a significant challenge in taking hundreds of accurate measurements “in-line” without delaying the production line.
Frost & Sullivan’s analysis of dimensional metrology systems in 2019 indicates Laser Radar technology as the “best in class” technology to provide in-line BIW inspections. Frost & Sullivan says that “Laser Radar is a fully automated, versatile system that brings non-contact measurement to the production line. It is a novel approach that includes direct surface and feature measurement with the capacity to perform 100% inspection checks. A Laser Radar system is surface independent, i.e., it can inspect most surfaces and is not sensitive to lighting or temperature. The latter is a big advantage of Laser Radar, especially for measurements in the production line. The system can operate without targets and make inspections with a very high level of accuracy. The system also scores well in its ability to be used in Pre-series production. Compared to other systems, Laser Radar can be applied in pre-series without the need for time-consuming fine-tuning of scan paths, adjustment of acquisition parameters, or lengthy off-line CMM correlations.”
API has closely watched the industry’s “in-line” BIW inspection goal. There are several major takeaways from interviewing industry experts familiar with the current Laser Radar technology and its inability to support in-line BIW inspection fully. The following attributes must be improved for automakers to meet the “in-line” inspection requirements—speed, accuracy, flexibility, portability, and repeatability.
New Inspection Technology
API’s Dynamic 9D LADAR (LAser Detection and Ranging) captures both dimensional and surface geometry data and incorporates technology that significantly improves automated production measurements. The patent-pending 9D LADAR offers a novel interferometry-based non-contact measurement system comprising Optical Frequency Chirping Interferometry (OFCI) technology. The OFCI technology uses 20 kHz speed fast laser chirping to generate a broad spectrum for optical interference. The interference signal yields 100x higher sensitivity than phase-detection methods.
9D LADAR uses APIs (patent pending) Optical Frequency Chirping Interferometer (OFCI) technology, developed over the last 15 years, with significant subcomponents designed for maximum performance and reliability. 9D LADAR provides micron-level resolution while eliminating issues associated with surface reflectivity, slow data acquisition speeds, limited accuracies, restrictive incident angles, and susceptibility to production environment noise.
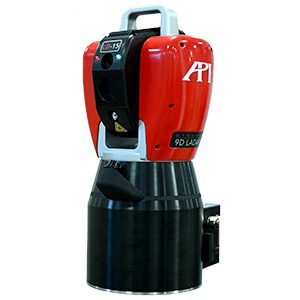
9D LADAR’s Enhancements Over Current Laser Radar Technology
Speed
- 9D LADAR systems process measured data at 20,000 points per second and with scanning speeds of 0.2 seconds/cm2. The current Laser Radar technology process’ measured data at 4,000 points per second and scanning speeds of 1.0 seconds/cm2.
Accuracy
- 9D LADAR’s linear accuracy at 12.5μm + 1μm/m versus Laser Radar’s linear accuracy at 20μm + 5μm/m
- 9D LADAR’s 3D accuracy is 6μm/m versus Laser Radar’s at 13.6μm/m
Flexibility
- 9D LADAR systems angular range at Azimuth: +/- 320⁰, 46⁰ – 69.4⁰ versus Laser Radar at Azimuth: +/-180⁰, Elevation: +/- 45⁰
- 9D LADAR can measure desired part features with up to an 85-degree incidence angle versus the Laser Radar at a 45-degree
Portability
- 9D LADAR’S compact design, weighing 10.4 kg, incorporates an integral controller with ethernet communication versus the Laser Radar at 29.9 kg with an external controller
- 9D LADAR’s overall dimensions, 191mm (W) x 254mm (L) x 432mm (H) versus the Laser Radar at 286mm (W) x 340mm (L)
Repeatability
- 9D LADAR’S repeatability average error is 35μm versus the Laser Radar at 150μm
APIs 9D LADAR outperforms conventional Laser Radar in Speed, Accuracy, Repeatability, Flexibility, and Portability.
Addressing the Laser Radar’s Inspection Speed Problem
Current Laser Radar systems must continually update their position in space every time they are moved to a new measurement position. One BIW vehicle can have several hundred required inspection points that must be measured from many different Laser Radar positions. Laser Radars are constrained by three factors that the 9D LADAR has overcome:
- Each time the Laser Radar moves to measure a required feature, it must reorient itself relative to the BIW. This process involves measuring several “tooling balls” with known positions, so the Laser Radar can always scan in the correct frame of reference relative to the BIW. The tooling balls are typically installed in an earlier process and must be protected throughout the inspection.
- The dramatic problem with the current Laser Radar technology is scanning speed. The current system scans at 1,000 points per second, compared to the 9D LADAR at 20,000 points per second.
- The last problem relates to incident angle capability. Current Laser Radar systems can achieve accurate measurements with an incident angle of 45 degrees. 9D LADAR can accurately measure parts with an incident angle of 85 degrees. This capability means 9D LADAR will need fewer measurement positions to acquire all required scans than the competitive Laser Radar.
API’s 9D LADAR and the 6DoF Radian Laser Tracker
To significantly reduce the cycle time inspecting BIW vehicles, API couples the robot-mounted Dynamic 9D LADAR with a 6DoF (Degrees of Freedom) Radian Laser Tracker. 9D LADAR mounted on the industrial robot is tracked in real-time using API’s 6DoF RADIAN Laser Tracker. API uses a unique 6DoF Sensor, called the i360, which is mounted directly to the 9D LADAR or attached to the robot. The exact 6DoF positioning of 9D LADAR’S measurements provides unlimited precision robot poses with little or no need to measure the time-consuming tooling balls that slow down the current Laser Radar technology.
With faster scanning speed, higher incident angle, higher data sampling, and 6DoF tracking, 9D LADAR’s total throughput is 3X – 4X higher than the current laser radar technology.
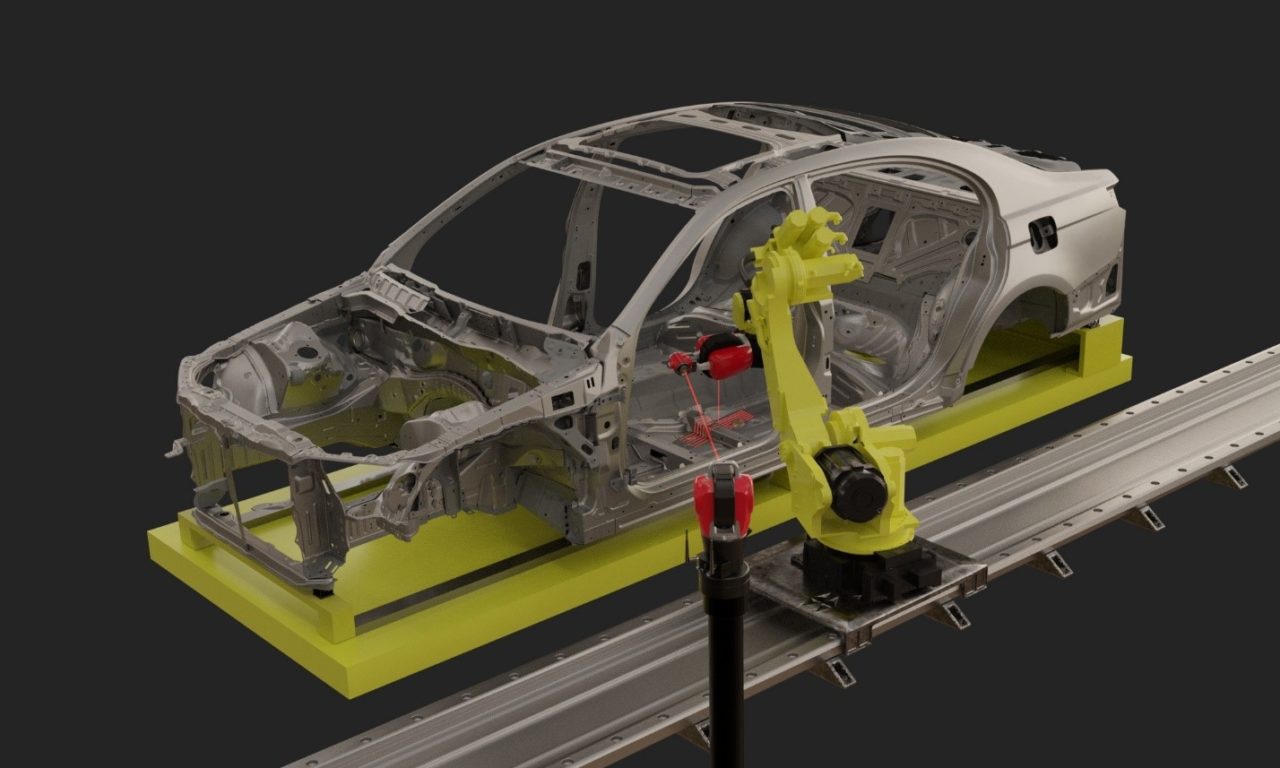
API Dynamic 9D LADAR measuring Body-In-White, while 6 DoF Radian Laser Tracker captures 9D LADAR’s position
While adding the Laser Tracker increases equipment costs, the option dramatically reduces the cycle time to inspect BIW vehicles over current Laser Radar systems.
Summary
Dynamic 9D LADAR coupled with Radian 6DoF Laser Tracker significantly improves overall throughput and cycle time. The overall accuracy, scanning speed, and minimized tooling ball measurements make this system capable of actual “in-line” BIW inspection.
9D LADAR significantly outperforms conventional Laser Radar technology in speed, accuracy, repeatability, flexibility, and portability. The addition of Radian 6DoF Laser Tracker further enhances the capabilities of an actual “in-line” BIW inspection system.
The auto industry’s BIW is just one example of this technological shift that will directly benefit manufacturers across every industry and provide a competitive advantage. Click here to learn more about 9D LADAR or fill out the form below to contact us and speak to a Real Metrologist today.