Radian Laser Tracker Calibrates Handan Rolling Mill
API’s Dimensional Metrology Equipment Improves Steel Plate Accuracy
Steel plate manufacturing is a multi-step process, often requiring multiple machine adjustments after the smelting process to roll the steel properly. Depending on the plate’s thickness and quality demands, mill operators need to adjust the bearings that control roller height or change out the rollers to create a different surface finish on the plate. These continual adjustments and installations wear on the machine and can threaten the tolerances required for the plates. Handan Iron & Steel Group is one of the largest producers of such plates in China, and they contacted API to help ensure the performance of their rolling mills and the quality of their plates. Using the Radian Laser Tracker and API’s team of expert metrologists, Handan was able to:
- Improve the acceptance rate of their roller installation to over 99%
- Increase productivity by 11%
- Perform real-time evaluation in harsh measurement conditions
Established in 1958 and located in the Hebei province of China, Handan Iron & Steel Group (Handan Steel) has total assets of over 85.6 billion China Yuan, and a staff of 24,000. Their annual production capability can meet 13,000,000 tons. Handan Steel is one of the most important steel production bases in China.
Yet, reaching nearly 100 billion in assets did not mean Handan Steel’s work was done, and they continued to look for ways to update their technologies to find better ways to produce higher-quality steel plates.
Aiming to find a more effective and accurate way to inspect and calibrate their rolling mill machines, Handan Steel’s engineers sought help from API, and API provided a set of solutions to Handan steel to update their calibration technology.
How do Rolling Mills Work?
Once the steel ingots come out from the smelt plant, they are still a semi-finished product. Only when the ingots are rolled by the rolling mill machines do they become the end product.
The steel ingots come out of the smelt plant, and the next step is to put the ingots into the rolling mill machine. As shown in Picture 4, the steel ingots go through the rolling mill while, the bearing controls the pressure of both rollers at the same time. After going through 8 groups of rolling mills, the steel ingots have been pressed into steel plates, and after cool down they are ready to be inspected as the end product.
Handan Steel’s Problem
There were two problems that troubled Handan Steel’s engineers when working:
- Because the rollers are under stress all the time, the position between the rollers and the roller housing may change after long time use. This change will trigger changes in the shape of the steel plates the roller’s produce, often leading to one side being higher or lower than the other.
- After long time use, the changes in position can begin to affect the flatness of the roller’s surface. This adds an additional uncertainty that can make the steel plate’s produced uneven or possibly out of tolerance.
API’s Solution
The Real Metrologists of API suggested Handan Steel’s engineers use the Radian Laser Tracker and software to resolve the problems mentioned above.
- To resolve the problem of the position difference between roller and roller housing, API recommended two steps. Firstly, Handan would use Radian to record several reference points on both roller and roller housing. Secondly, they would use these reference points to mark a standard position relationship between the roller and roller housing, and then compare the actual position of the roller to the standard roller position in the software to figure out what values need to be adjusted. Then, Handan’s engineers would use this value to adjust the roller’s position back into tolerance.
- To resolve the roller’s surface flatness problem API proposed Handan use Radian to collect several reference points on the surface of the roller, and then use these points to make a standard cylinder in the software. After this, Handan could compare the actual value to the standard value to figure out what parameters need to be fixed or maintained to guide repairs of the roller surface.
Using Radian to execute these proposed solutions, Handan has improved the acceptance rate of their roller installation to over 99% and has increased productivity by 11%.
Stability in Harsh Environment
While measuring at Handan Steel, API’s Radian Laser Tracker has delivered perfect performance, and shown its ability to adapt in harsh working environments. The process of steel rolling and milling requires pouring water on the hot steel to cool it down. Therefore, the air inside the plant is full of steam. As a precision measuring instrument, however, even under such harsh conditions, Radian can work in stability. Relying on its self-protecting level and weather sensor, Radian can work under in humid environments without condensing.
The weather station performs as another important role. The sensors of Radian’s weather station detect the status of the environment in real-time and give feedback to Radian to compensate the values in real-time. All of these features guaranteed the stability an accuracy of Radian in Handan’s plant.
API’s unique combination of state-of-the-art equipment and Real Metrologists with expertise in applications across all fields delivered the complete metrology solution Handan was looking for. Click here to learn more about API’s portable equipment and contact our Globally-Local team.
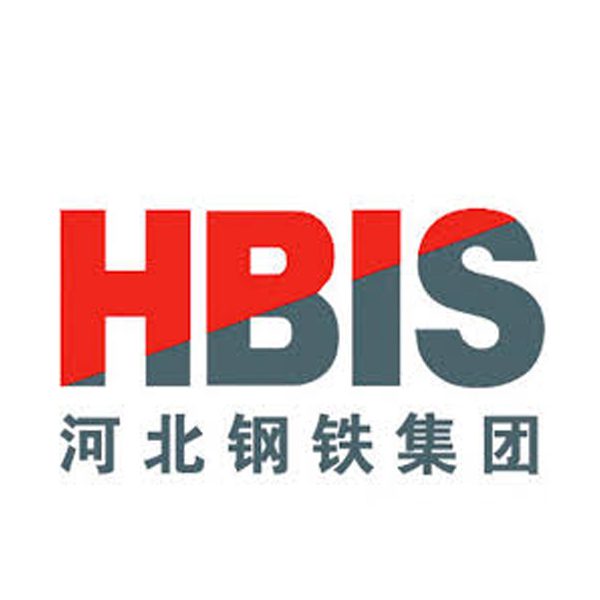
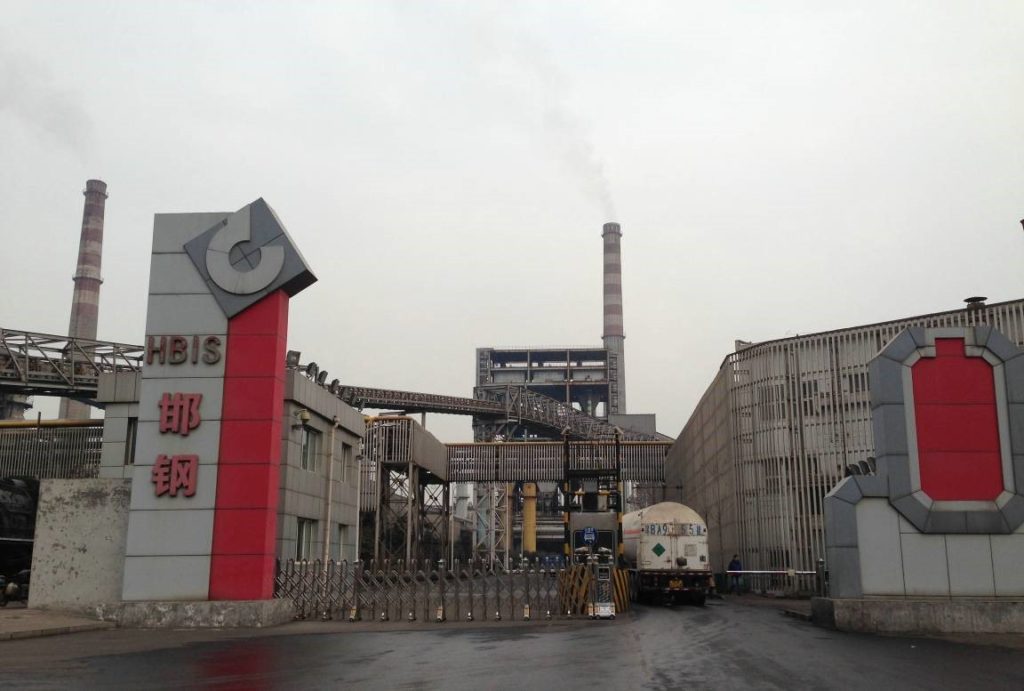
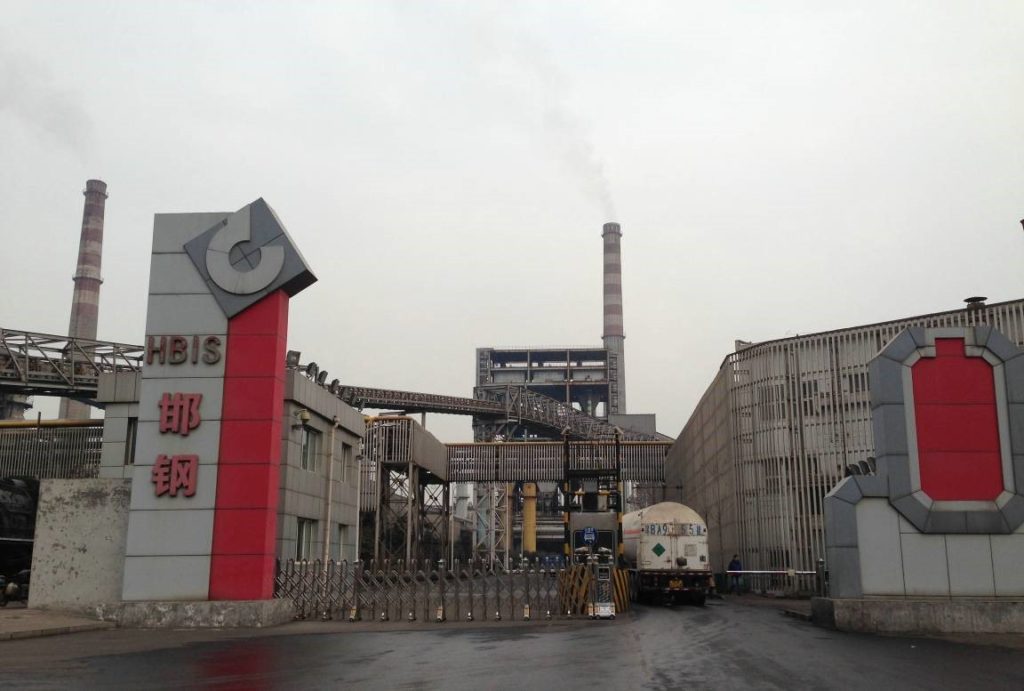
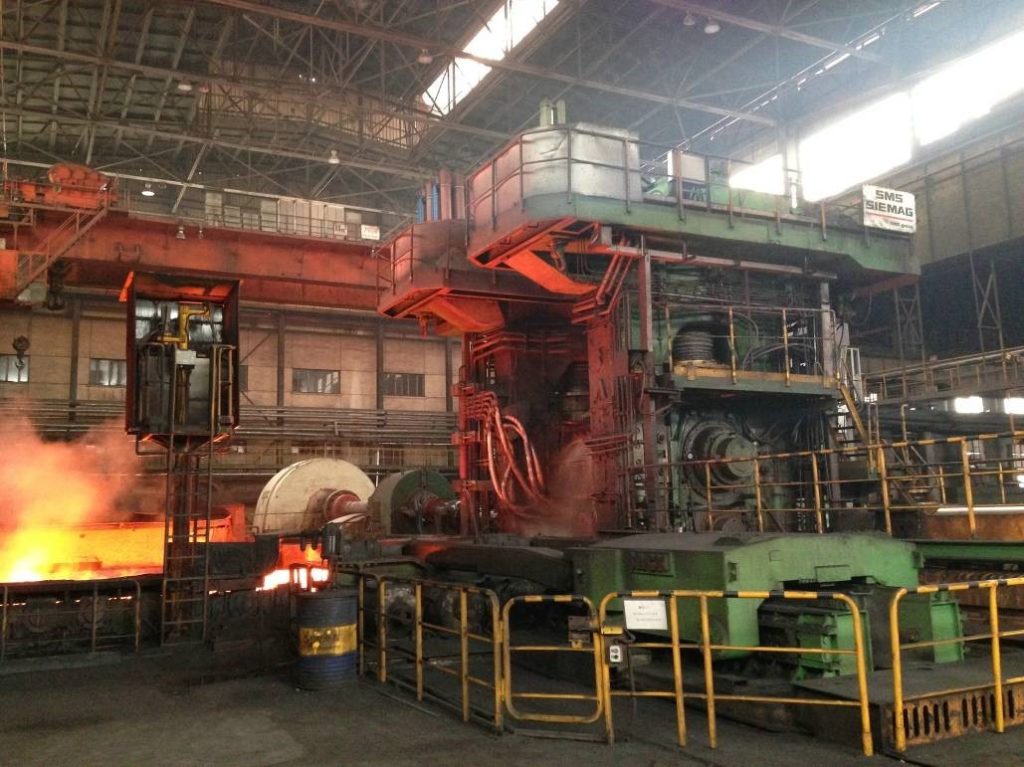
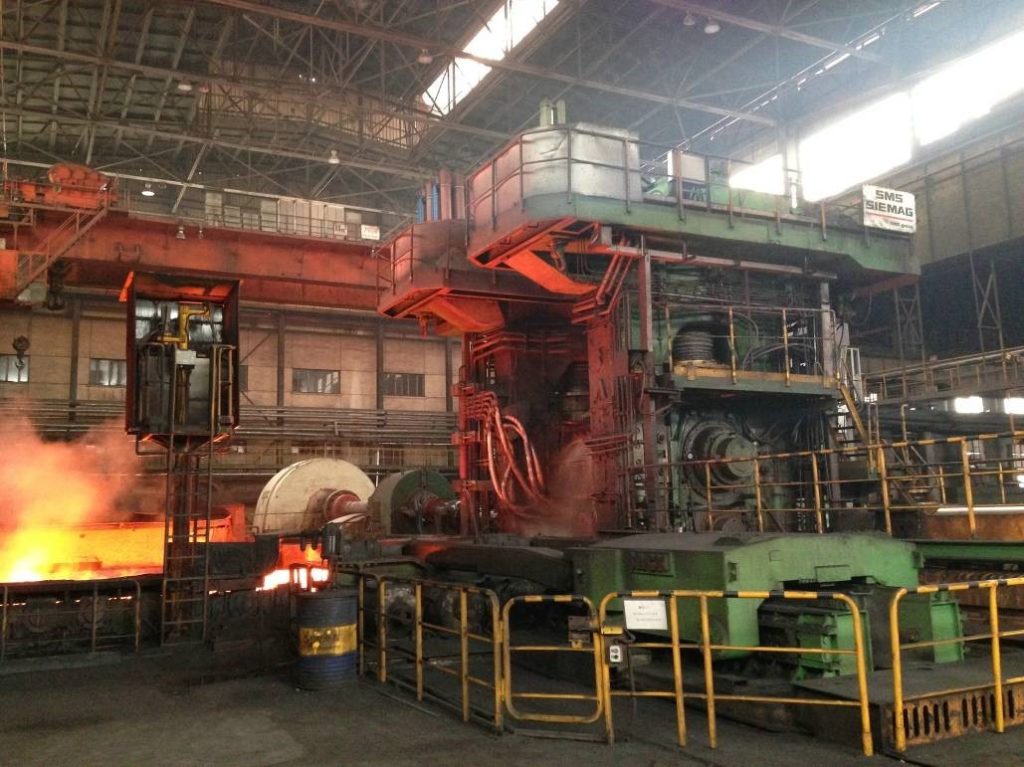
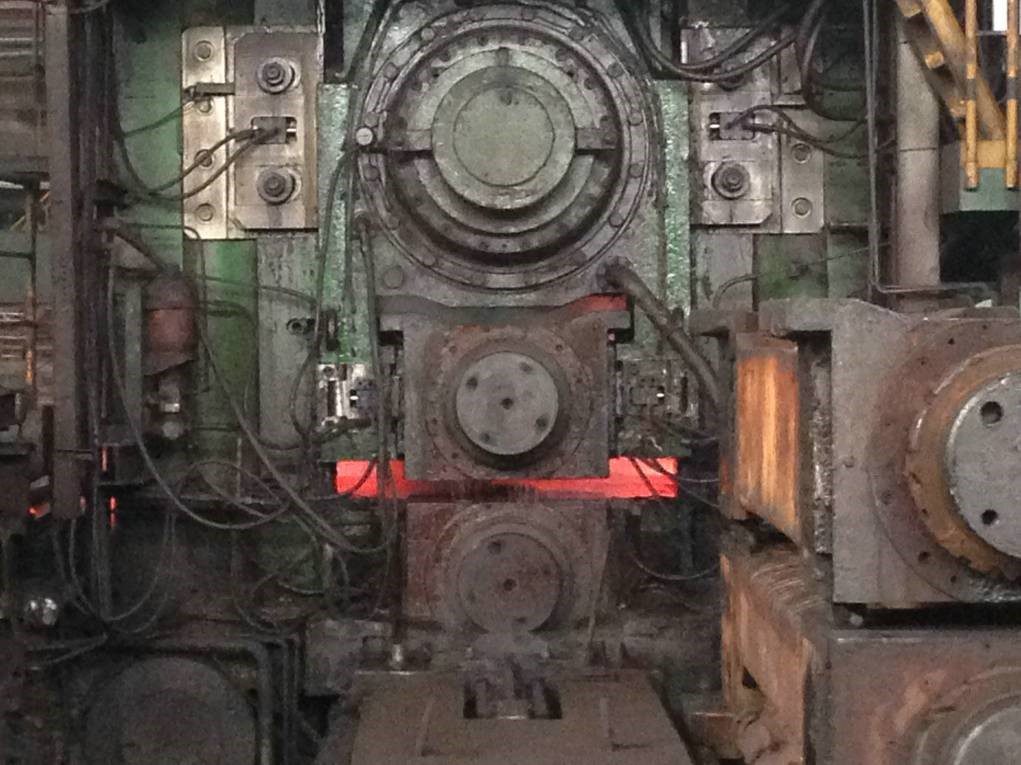
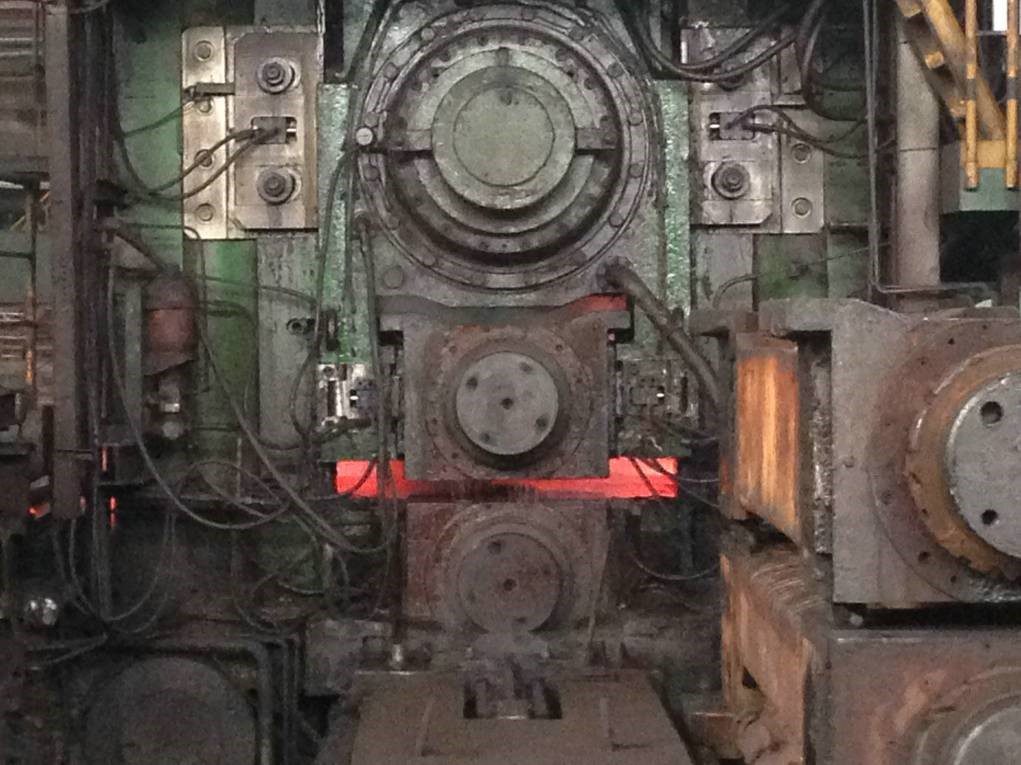
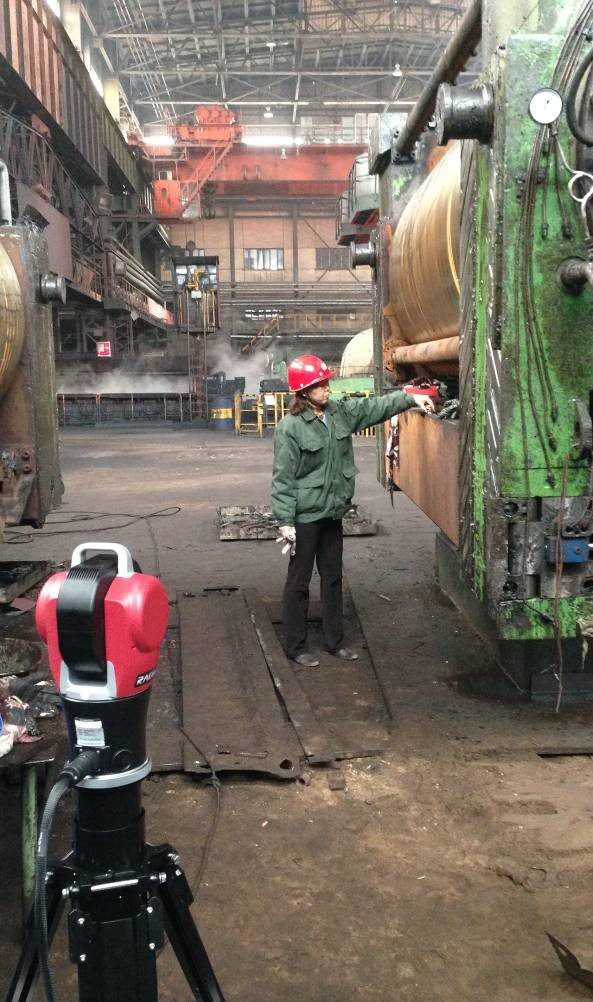
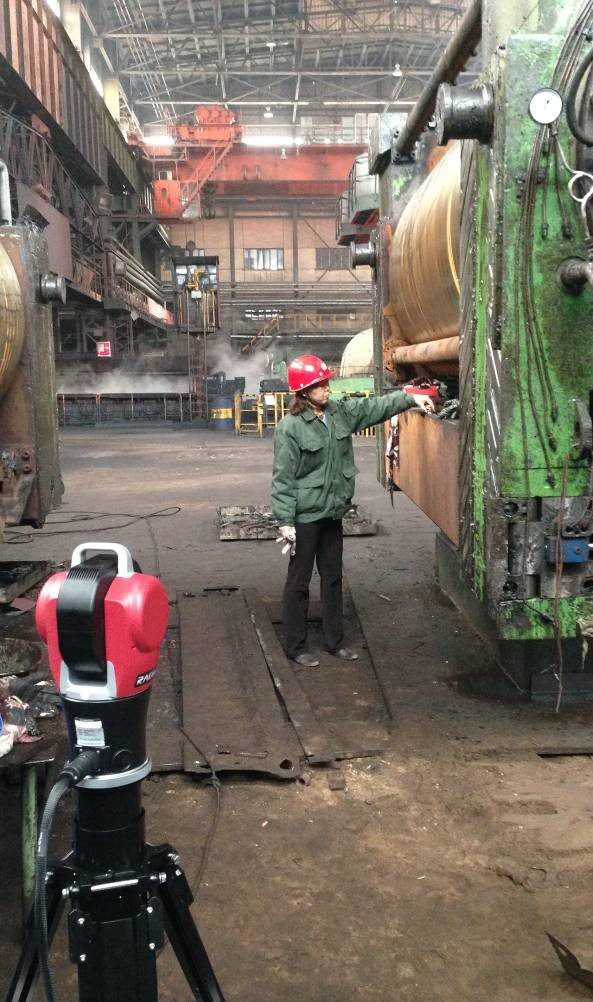
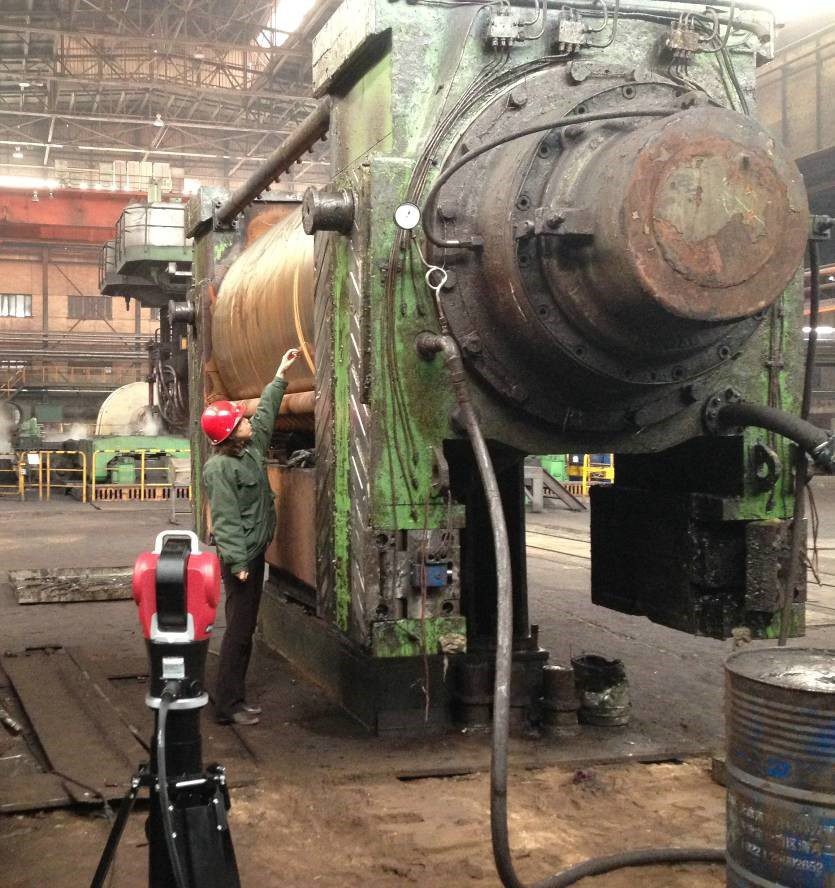
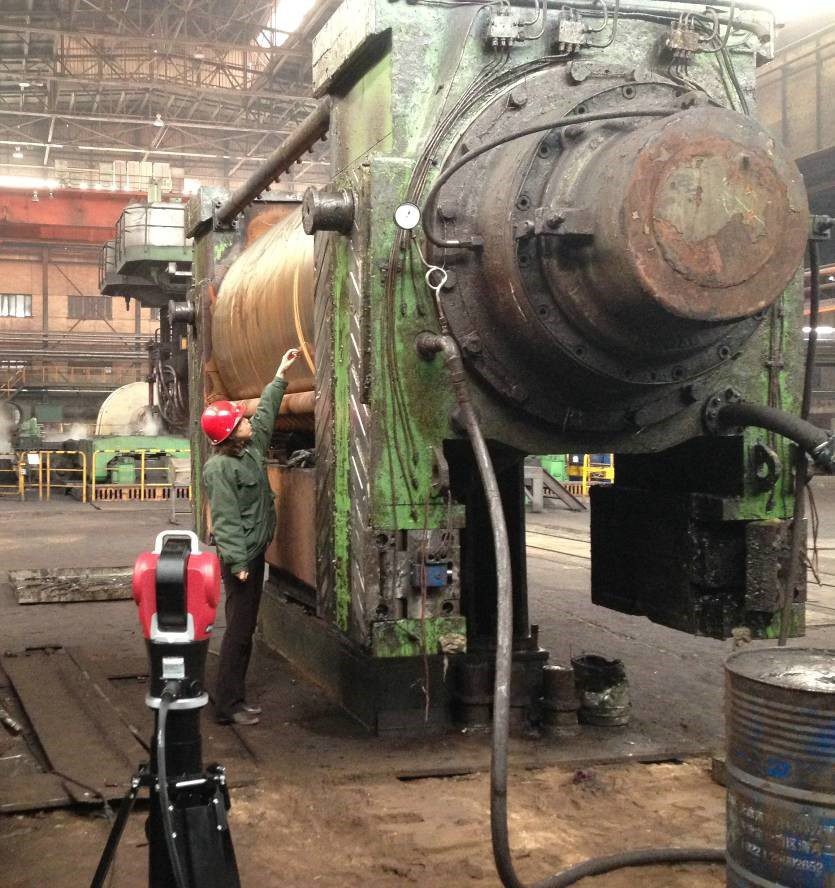