Radian Plus Verifies Lithium Battery Manufacturing Process, Maximizes Efficiency
API’s 6DoF Laser Tracker Captures All Errors in Simple Measurement Setups
Since the invention commercial lithium batteries, the technology has been applied to many fields of manufacturing, and they have rapidly developed, marking a milestone role in the progress of global human science and technology. Compared with normal batteries, lithium batteries have higher energy storage density, longer service life, higher rated voltage, better endurance of high power, better charged maintenance ability (low self-discharge rate), wider temperature scope, and green energy (as their production, use and scrap, does not contain or produce any poisonous and harmful heavy metals such as lead, mercury, cadmium).
With accelerated demand from the global manufacturing industry and stricter environmental protection requirements, the application of lithium batteries has gradually expanded or deepened to various fields including green energy vehicle manufacturing, portable digital products, portable power tools, aerospace electromechanical, military communications, and many others. Therefore, the global lithium battery manufacturing industry has also entered a stage of rapid growth. And when a leading lithium battery producer needed a way to quickly verify their processes to maintain speed and accuracy in production, they contacted API. Using Radian Plus, the experienced team of Real Metrologists at API was able to create a simple solution that allowed the manufacturers to:
- Ensure machine accuracies to within .1mm
- Measure the entire 30m range of the coating machine
- Run error reports and make adjustments in real-time
A leading lithium battery manufacturer located in China’s Yangtze river delta region reached out to API to help support their processes. Their lithium batteries are produced for quality and used by customers from China to America to Europe to Australia.But they were facing large production scales and strict production standards and needed to guarantee product quality while maintaining production efficiency. Regular inspection and evaluation of production equipment would provide objective, scientific, and reliable data support for these purposes.
Manufacturing Process
The process of lithium battery production is generally divided into three procedures: first the “coating” and “rolling” stage, second the “winding” stage, and third the “forming and packaging” stage. API’s Radian Laser Tracker provides evaluation and guidance data for the production equipment in each of these stages, which provides a strong guarantee for the smooth implementation of each process.
For these three stages, manufacturers need to meet several requirements, including:
- The flatness error of the main plane structure of the winding machine is less than 0.1mm.
- The parallelism error between the rollers (coating machine and rolling press machine) is less than 0.2mm.
- The flatness accuracy of the all-in-one production machine’s substrate is less than 0.1mm.
- The installation guidance of a newly installed coating machine production line, requires providing all-round and high-precision data support within a long range of more than 30m, and guiding the placement of irregular parts and rollers.
API Solution
To fulfil the customer’s needs, API recommended purchasing Radian Plus; Radian Plus provides micron level 3D measurement accuracy, which could fully meet customer requirements for error measurement accuracy, and the use of wireless data transmission and a battery power supply system, with flexible installation features, provides a combination of efficiency and accuracy. Once onsite with, Radian Plus, API was able to showcase how these measurements would work in production.
During the measurement:
- Radian Plus was set up next to the winding machine to be measured. By using the Spherically Mounted Retroreflector (SMR) to touch the points to be measured on the plane structure of the machine, the 3D position of these points is obtained by the Laser Tracker; after this, the software set up a standard plane, which then compared the collected data with the standard plane, and determined the flatness error.
- After selecting a good position to set up Radian Plus, the SMR collected data points on the surface of the press rollers to be measured. Using this data, the structure of the press roller was fitted in the software, and the central axis was calculated as well. By comparing the parallelism between the central axes of each press roller in the software, the parallelism error between the press rollers was obtained.
- Measuring the flatness error of the substrate of the all-in-one machine was similar to the flatness error measurement of the winding machine’s plane structure. Setting up the Laser Tracker in an appropriate position, the SMR touched the substrate and collected the points’ 3D position and recorded it in the software. Then a standard plane was setup in the software to compare the actual collected data with the nominal value on the standard plane, and the flatness error could be analyzed.
- The length of coating machine production line is more than 30 meters; Radian Plus has an 80 meters measurement radius, and this perfectly covered the whole length of the coating machine. Moreover, the actual measurements verified the fitting accuracy of the transfer station better than 0.047mm, which fully met the manufacturer’s demand of “providing all-around and high-precision measurement data”.
As an advanced, accurate and efficient precision measurement solution, API’s Radian Plus Laser Tracker provided an objective and trustworthy data guarantee for each process of lithium battery production. Radian’s measurement accuracy at the micron level can fully meet manufacturer requirements for the verification of production equipment. While guaranteeing high precision measurement, Radian Plus also shows dynamic guidance functions, which makes real-time adjustment possible. The AutoLock feature is especially convenient for wide range measurement operations, as the tracker can quickly lock the laser beam to the SMR in the operator’s hand over long distances (even in dark environments), so that the operator does not have to worry about losing the laser beam and can focus on the measurement itself.
To learn more about Radian Plus, or API’s other dimensional metrology equipment and services, please fill out the form below to contact us today.
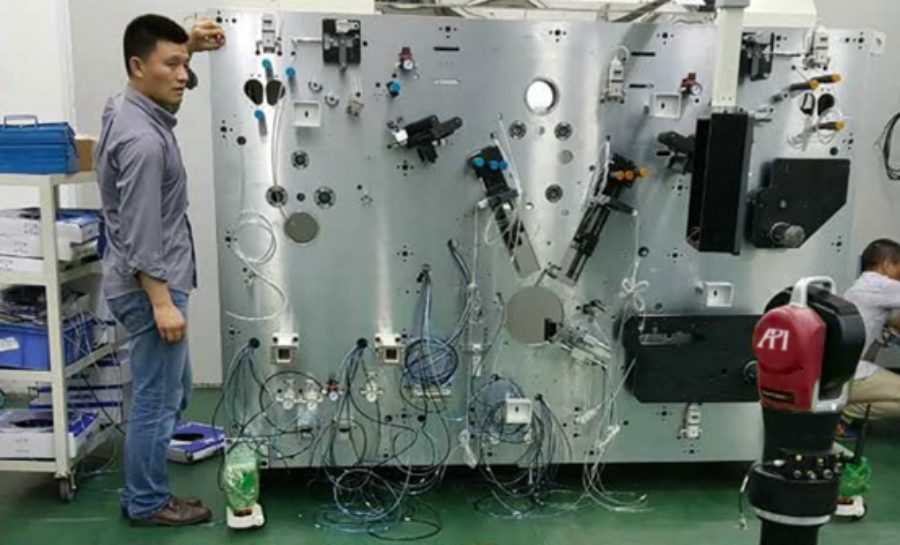
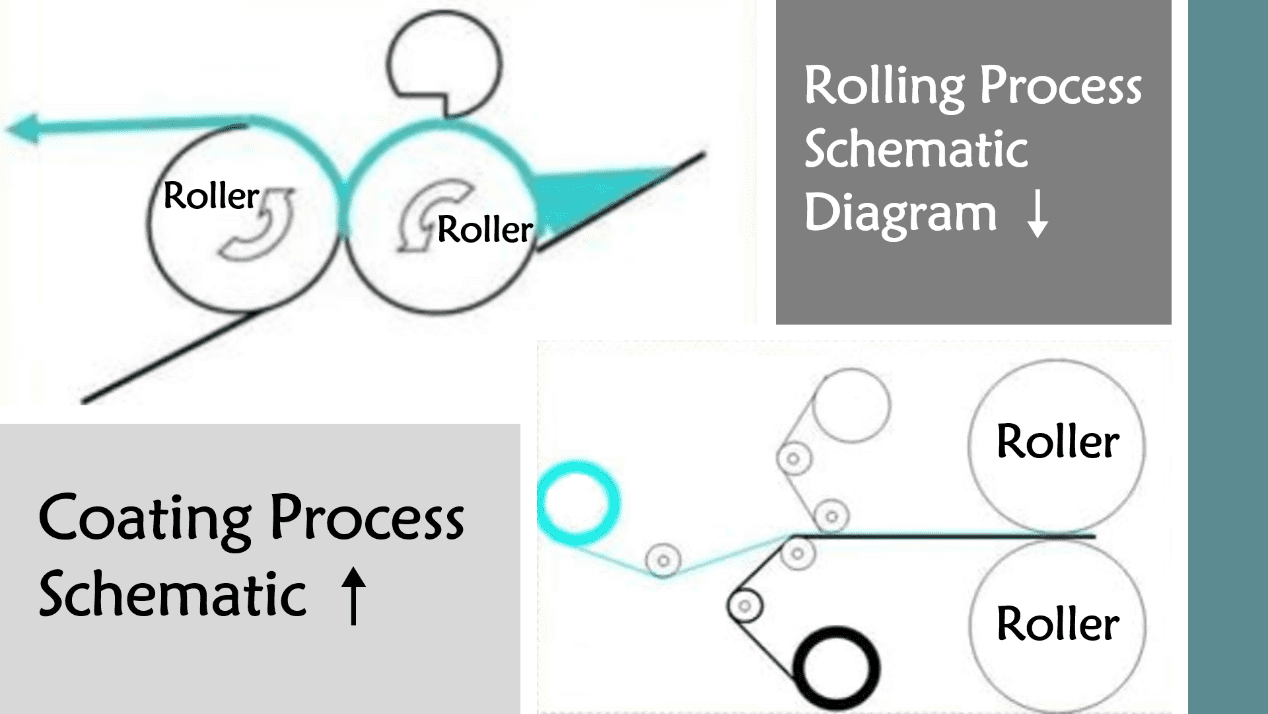
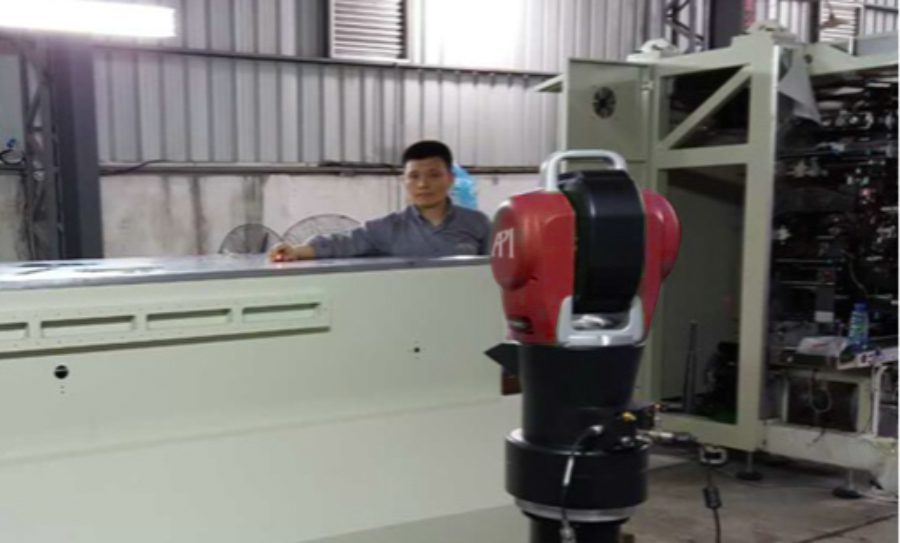
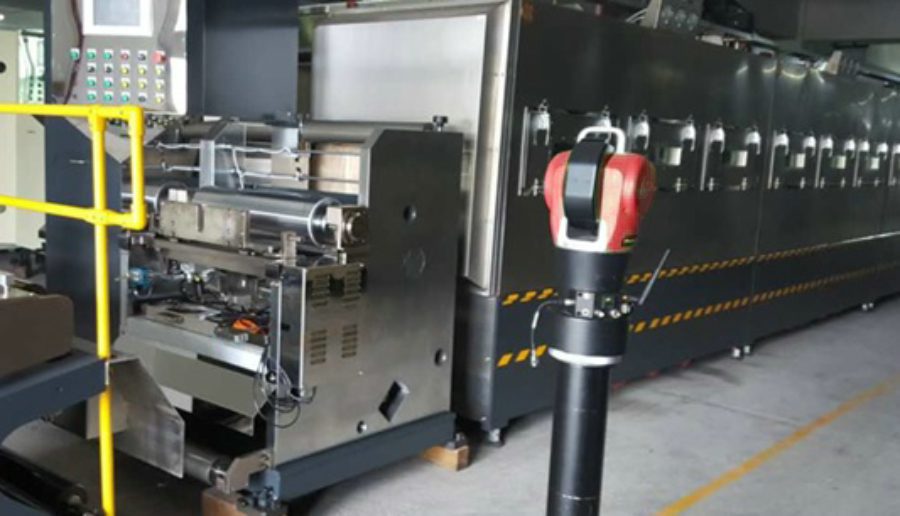